Laser Beam Welding of Titanium Alloys
In recent years, there is an increased in used of titanium alloys for some parts of mass-produced automobiles and aerospace. However, titanium alloys are characterized by difficult machinability, high melting temperature, high strength, low thermal conductivity, and high reactivity to oxygen, which overshadowed conventional manufacturing processes. To this end, there is a pressing need for more efficient technologies for the manufacture of low-cost titanium structures. Over the years, several joining techniques have been considered for fabrication of titanium alloys. Nevertheless, laser beam welding presents a viable option for welding of titanium due its versatility, high specific heat input, and flexibility. To date, under optimum processing conditions, the strength of the laser-welded titanium alloys can be close to the original material; however, there are still some processing problems such as lower elongation and corrosion resistance coupled with inferior fatigue properties.
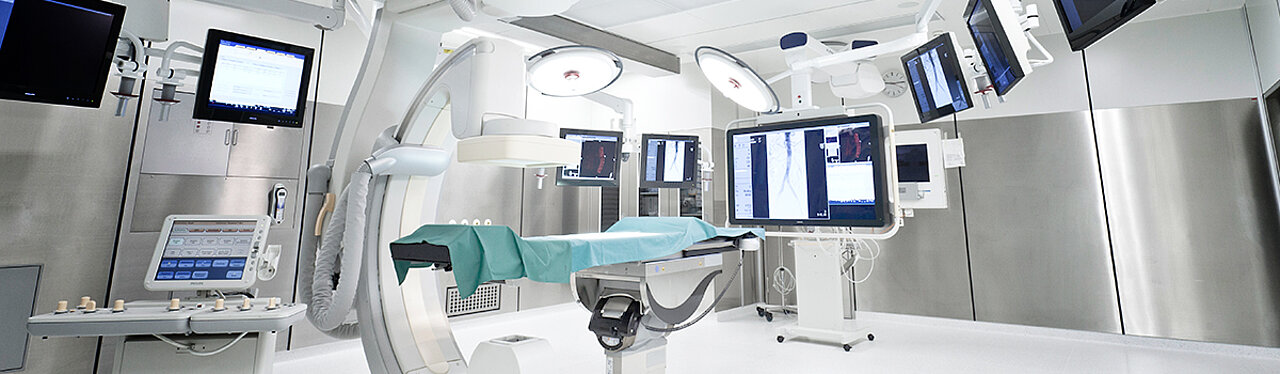
Titanium: a Challenge to Weld
Titanium is a super light weight metal with excellent corrosion resistance and the highest strength-to-density ratio of any metallic element. It’s a great material for many applications, from super light weight aerospace parts to artificial joints to implanted medical devices.
Titanium has two properties that greatly influence its weldability:
1) Titanium has a great chemical affinity for combining with oxygen; and
2) Titanium doesn’t have a great affinity for combining with any other chemicals.
In open air, freshly machined or cleaned titanium quickly forms a microscopic layer of oxides. This formation of oxides creates a natural passivity that inhibits the reactions with other chemicals, such as salt or oxidizing acid solutions. The result is that titanium has superior corrosion resistance. However, when heated for welding, these oxides form even faster, and as the temperature reaches titanium’s melting point (1668 °C), the oxides dissolve into solution and contaminate the weld pool, causing an impure and very weak weld. For this reason, special care must be taken to minimize the weld piece’s exposure to oxygen after cleaning and during welding.
Laser beam welding is a good option for welding titanium. If part cleaning and gas cover are handled properly, the process will yield high quality welds at a reasonable cost. Typically, laser welding penetration can range up to 6 ~8 mm in titanium (3~4 mm for 2kW fiber wobble laser) For deeper penetration welds or more difficult applications, we recommend using electron beam welding.
Pre-Weld Preparation of Titanium
Titanium is a hard metal, so special machining precautions during fabrication are not necessarily required, but as with all precision welding applications, special care must be taken to remove oxides and hydrocarbon contamination from titanium parts before welding.
- This is can be achieved mechanically, using stainless steel wire brushes, grinding, filing or scraping to remove any oxides.
- There are also chemical cleaning methods utilizing immersions in caustic solutions and water that are effective at removing oxides.
Hydrocarbon residue on titanium parts is usually removed using acetone or alcohol based solvents. Avoid using chlorinated solvents in the welding area because they can form toxic gases when heated.
Titanium parts should be welded immediately after cleaning.
If this isn’t possible, parts can be sealed in plastic bags back filled with dry argon or nitrogen
to avoid having to repeat the cleaning process.
Joint Preparation Guidelines for Welding of Titanium
- When cleaning a surface with solvents, use clean cloth such as cheese cloth or paper towels. Do not use shop rags that may be contaminated with oil residue.
- Use a stainless steel wire brush to clean a joint only after solvent cleaning. Wire brushing prior may embed hydrocarbons and other contaminates.
- Always use a new or recently cleaned stainless steel brushes to clean a joint. Older brushes sitting around a work bench may contain oils and other contaminates. Do not use brushes that have been used on other metals as metal flakes can be carried on the brush bristles and cause contamination and weak welds.
- Use a stainless steel wire brush to clean any metal surface that has been etched. By-product residuals from etching can alter the chemical composition of the weld pool, resulting in a weak weld.
- Clean all wire brushes and cutting tools frequently.
- Avoid using compressed shop air to blow off debris from the area of the joint. Compressed air contains moisture and oil contaminates. If a part must be blown off, use a bottled gas such as nitrogen or argon.
Fixturing Titanium parts for Laser Welding
Laser welding requires a precise joint in order to maintain permissible gap and avoid mismatch.
Good weld fixturing is necessary so that the laser beam can be placed accurately.
Of course, the most accurate laser welds happen when beam placement and welding process are computer or Robot controlled rather than manually controlled.
Shielding gas for Laser Welding of Titanium
Gas coverage for Titanium Laser Welding
Generally, a shield gas such as argon or helium is used to protect the part, and special care must be taken to make sure the gas completely covers the heat affected area including the back side and/or interior of the part.
- One option that provides exceptional gas coverage would be to weld the part in a laser welding glove box filled with pure gas.
- Parts can also be reliably welded in a full vacuum (as is the case with electron beam welding), however, laser welding in a vacuum not widely available.
Since titanium is a very non-reactive substance, it is an excellent material for use in medical applications in which it will be in extended contact with human tissue, because chemicals and compounds within the body simply don’t bond with titanium. However, this characteristic also means that titanium does not easily alloy with other materials, which makes it almost impossible to weld titanium to any other metal. Hence, it is not recommended to use titanium in any dissimilar material welding application.
Cover gases are absolutely required when laser welding titanium. Special care should be taken to insure the heated area of the part are completely covered with gas. Simply directing a gas nozzle in the area of the weld will not provide adequate coverage. Special tooling or fixtures should be utilized to completely flood the weld and surrounding area with gas. A pure gas laser welding glove box is the optimal setup for welding titanium.
Choices of cover gases are limited:
- Argon: the relatively low cost of the gas make it the first choice for most titanium laser welding applications. Additionally, because it is slightly heavier than air, Argon is easy to direct and cover a part — Argon tends to stay in the weld zone.
- Helium: generally not recommended due to its high cost. Helium is considerably lighter than air, making it difficult to contain and direct. However, helium cover gas tends to provide a hotter weld pool, allowing for potentially deeper penetration.
- Argon-Helium Mixtures: generally recommended when a range of characteristics is required by the application.