Copper Welding
PhotonWeld series breaks through the copper welding bottleneck and opens a new chapter of efficient copper welding
Copper is a metal element known for its ductility and malleability, primarily existing in monovalent and divalent forms in compounds. As a prominent conductor of heat and electricity, copper is naturally occurring and widely found in various ores such as brass ore, chalcopyrite, bornite, cuprite, and malachite. It is utilized in industries, engineering technologies, and craftsmanship in metallic form or as alloys. Being a super highly reflective material, welding copper has been a challenging technological hurdle, especially in industries that involve welding copper components, where ensuring both the solidity and smooth appearance of the weld seam is crucial.
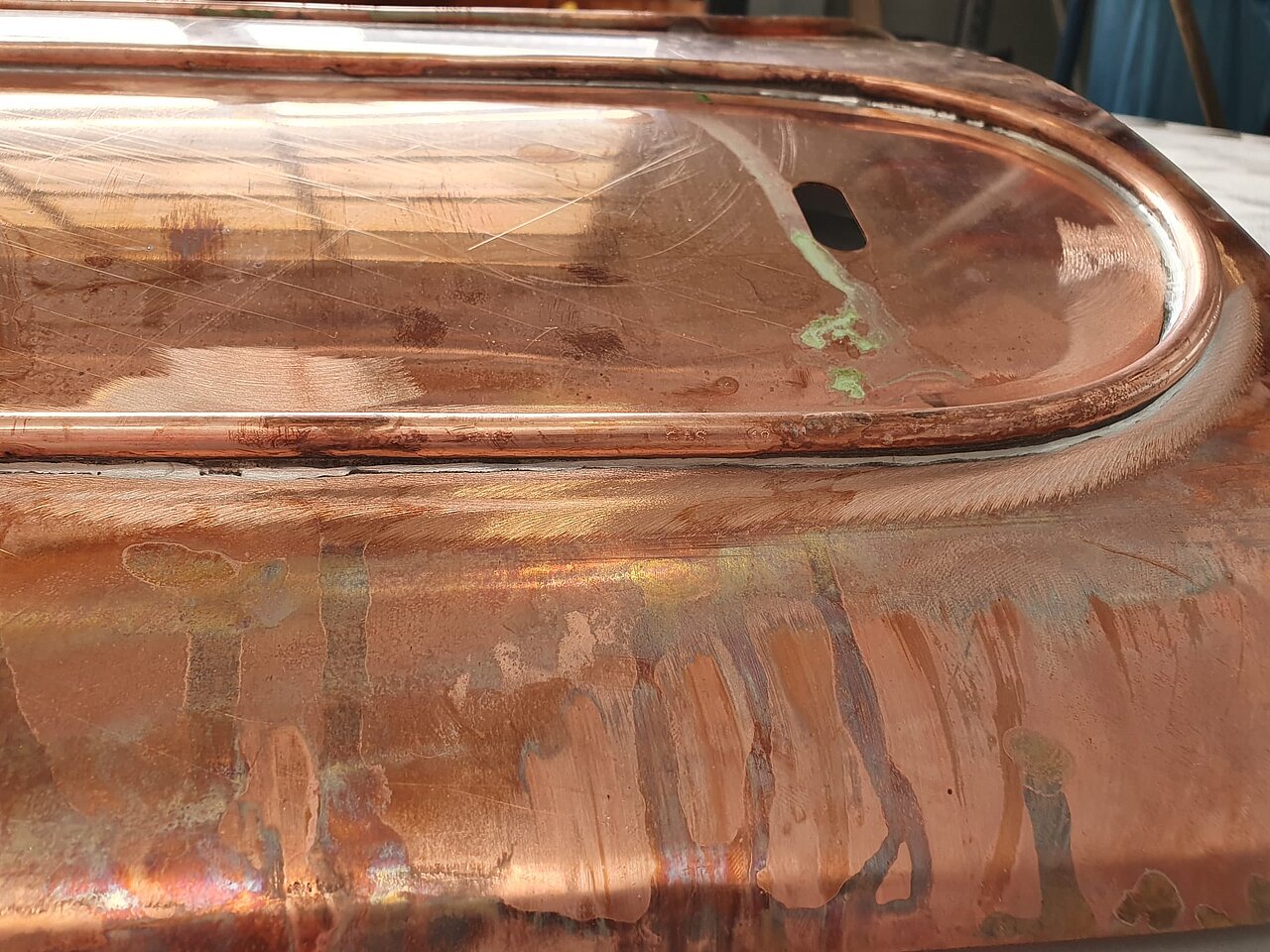
Challenges in Copper Welding
Copper, a common metal material with excellent conductivity and thermal properties, finds extensive applications in electronics, electrical engineering, construction, and manufacturing. With the continuous improvement of production demand, the application of laser handheld welding in copper welding has become a hot spot for manufacturers.
Users still need to polish their skills when they want to choose a handheld welder that is truly suitable for copper welding. If you want to choose a suitable handheld welder, you must understand the difficulties of copper welding as welding copper poses several challenges, including:
- High Thermal Conductivity
Copper's extremely high thermal conductivity means that heat easily spreads throughout the workpiece during welding. This requires higher welding temperatures and shorter welding times to ensure thorough melting of the welding area without excessive heating of the entire workpiece.
- Oxidation Issues
Copper readily reacts with oxygen to form an oxide layer, adversely affecting the welding process. The presence of an oxide layer can degrade the quality of the weld seam, reducing welding strength. Precautions such as using nitrogen or other shielding gases are often necessary before welding to prevent oxidation.
- High Melting Point
Copper has a relatively high melting point, necessitating the use of high-temperature welding equipment. Careful control of the welding temperature is required to avoid heat damage to equipment and work piece surfaces.
- Differential Thermal Expansion
Compared to other metals, copper has a relatively high coefficient of thermal expansion. In welding composite materials or dissimilar metals, differences in thermal expansion coefficients may lead to residual stress and deformation, requiring special attention.
- Welding Residual Stress
Due to significant temperature changes during welding, copper is prone to welding residual stress. This stress can result in part instability or cracking, making post-weld heat treatment and proper cooling essential.
- Material fusion is difficult
Due to the strong thermal conductivity of copper , the heat in the welding area will dissipate quickly , and the overall heat-affected zone of the welding part is also large, making it difficult to fuse the materials together;
- Material is easily deformed
Since the linear expansion coefficient of red copper is very large , once the temperature is too high during the welding process, the material will easily deform , which will test the welding skills;
- Prone to pores
When welding red copper, pores are prone to appear due to the influence of hydrogen and oxidation and reduction, which is more serious during deep penetration welding .
- High laser reflection
Red copper has a very low absorption rate of near-infrared laser at room temperature, so most of the incident laser will be reflected during the welding process, resulting in severe energy loss of red copper during the laser welding process, low laser energy utilization, and large lens loss. It will also shorten the service life of handheld welding.
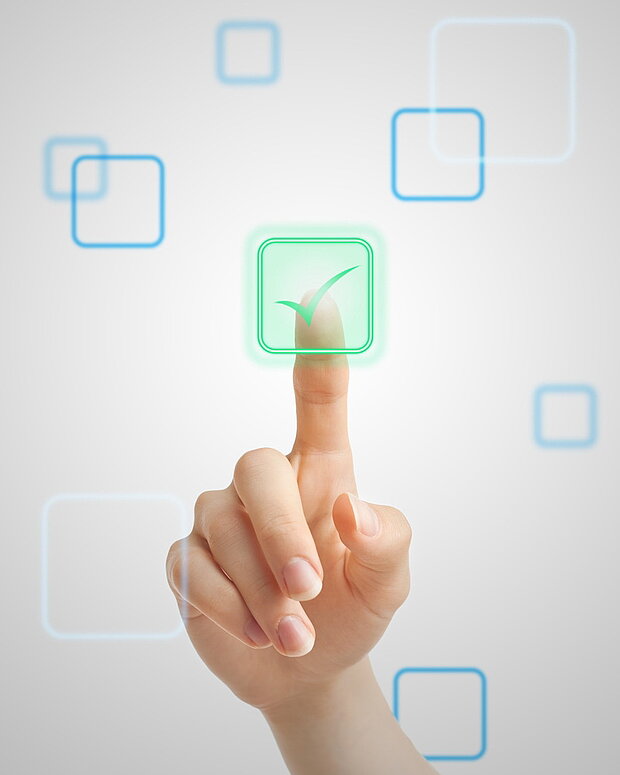
Common Copper Welding Methods
PhotonWeld A-Pro is the best choice and solution for Copper laser Welding
There are various methods for welding copper, and the choice depends on specific application requirements and work-piece characteristics. Some common copper welding methods include:
Resistance Welding
Resistance welding utilizes the heat generated by electric current passing through the work pieces to melt the surface momentarily, followed by applying pressure to join the two pieces together. This method is commonly used for welding copper wires and electronic components.
Gas Metal Arc Welding (GMAW)
Also known as Metal Inert Gas (MIG) welding, GMAW is a prevalent semi-automatic or fully automatic welding method. In GMAW, an arc is formed between the welding gun and the workpiece, heating and melting the copper welding wire, while an inert gas (usually argon) is used to shield the weld seam, preventing oxidation.
Arc Welding
This includes manual metal arc welding (SMAW) and tungsten inert gas welding (GTAW). SMAW uses a welding machine and welding rod, while GTAW employs inert gas (usually argon) as a shielding gas. These methods can be suitable for various thicknesses and shapes of copper.
Plasma Arc Welding (PAW)
Plasma arc welding is a high-energy density welding method suitable for thicker copper materials. In PAW, a plasma arc is generated using inert gas, and the energy of the plasma flow is controlled to melt the work piece surface.
Laser Welding
Laser welding is a highly precise welding method suitable for applications with stringent requirements for welding quality and appearance. Laser welding can achieve a very small welding heat-affected zone, minimizing deformation and welding residual stress.
Ultrasonic Welding
Ultrasonic welding involves momentarily melting the work piece surface through ultrasonic vibrations, followed by cooling and solidification to achieve welding. This method is suitable for applications sensitive to heat.
When selecting the appropriate copper welding method, factors such as material thickness, shape, quality requirements, and production efficiency need to be carefully evaluated and considered. Different welding methods have their advantages and applicability, necessitating a thorough assessment in practical applications.
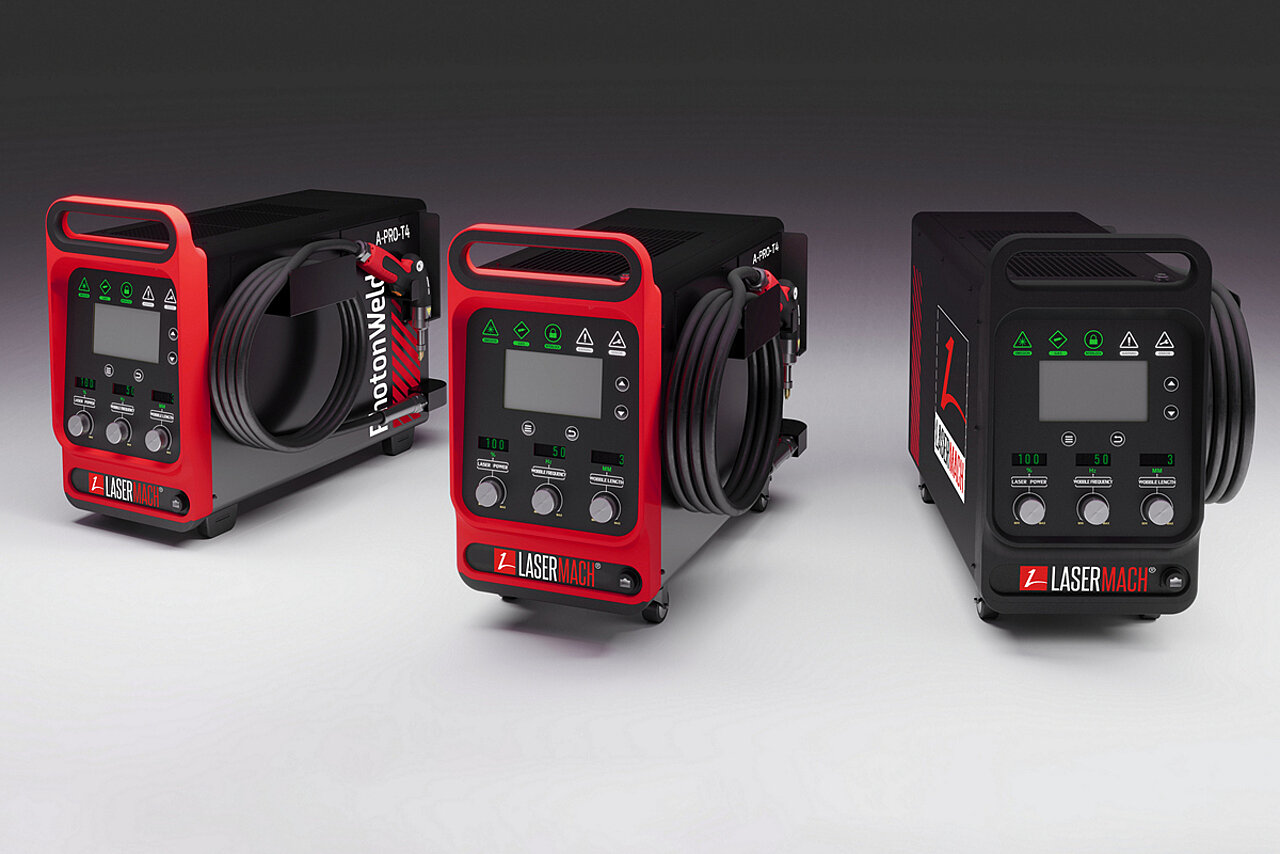
Principles and Advantages of Laser Welding Machine for Copper Materials
The application of laser welding machines in welding copper materials offers significant advantages, making it an ideal choice for specific applications:
Laser welding is an efficient and precise welding method that utilizes a high-energy density laser beam as the heat source. It represents a crucial aspect of the application of laser material processing technology. Initially used in the 1970s for welding thin-walled materials and low-speed welding, laser welding is a type of heat conduction welding. By controlling parameters such as laser pulse width, energy, peak power, and repetition frequency, the work piece is melted, forming a specific molten pool. In this process, the laser radiation heats the surface of the work piece, and the surface heat diffuses inward through heat conduction. Due to the high energy density, low deformation, narrow heat-affected zone, high welding speed, ease of automatic control, and elimination of post-processing, laser welding has become an essential means of metal material processing and manufacturing in recent years. Its applications span across industries such as automotive, aerospace, shipbuilding, hardware, medical devices, batteries, sensors, and home appliances.
The application of laser welding machines in welding copper materials offers significant advantages, making it an ideal choice for specific applications:
- High Energy Density
Laser welding machines generate a beam with high energy density, allowing rapid energy transfer during the welding process. This facilitates quick heating of the welding seam area to achieve fast and efficient welding.
- Small Heat-Affected Zone
Due to the concentration of energy in a small area, laser welding produces a relatively small heat-affected zone. This helps reduce thermal deformation of copper materials and minimizes welding residual stress.
- Precision Control
Laser welding provides precise welding control, enabling highly accurate adjustments to welding depth, weld seam shape, and welding speed. This is crucial for applications with high requirements for welding quality and appearance.
- Non-contact Welding
Laser welding is a non-contact welding method, with no electrode directly touching the workpiece surface. This helps avoid introducing external impurities and reduces electrode wear, especially suitable for applications requiring weld seam purity.
- No Filler Material Required
In certain cases, laser welding can achieve welding without the need for filler materials. This is advantageous for applications that demand impurity-free and defect-free weld areas.
- Suitable for Complex Shapes
Laser welding is applicable to welding workpieces with complex shapes, as the laser beam can be flexibly positioned and moved along a predetermined path, adapting to various welding requirements.
- Remote Operation
Laser welding machines can be remotely controlled through Computer Numerical Control (CNC) systems, allowing operators to monitor and adjust the welding process in a safe environment.
While laser welding offers numerous advantages in welding copper materials, factors such as high equipment and energy costs, as well as the specialized requirements for operators, need to be considered. Therefore, when choosing a welding method, a comprehensive assessment of specific application requirements and practical considerations is essential.
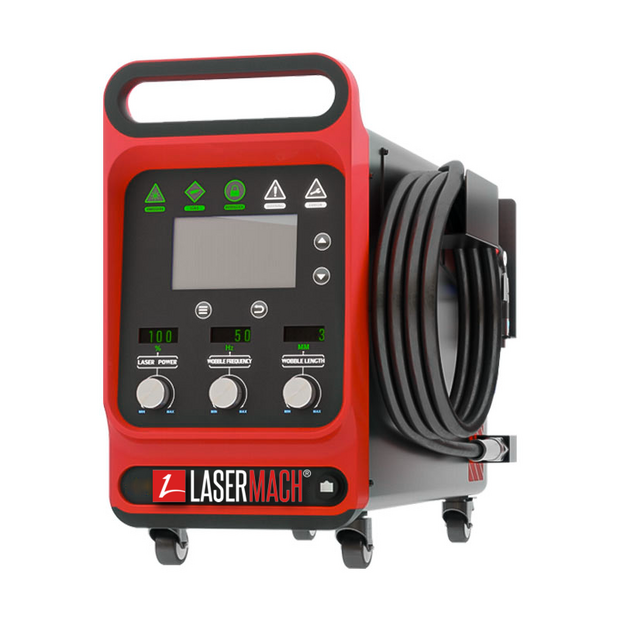
PhotonWeld A-Pro series of handheld laser welders always puts customers' needs first and provides customized solutions for the difficulties in copper welding applications.
Laser energy density and resistance to high reactive energy are the keys to copper welding.
In the debugging and use of end customers, the PhotonWeld A-Pro series showed excellent performance in copper welding:
Copper has fast heat conduction and high reflectivity. Laser energy density and resistance to high reactive energy are the keys to copper welding.
The PhotonWeld A-Pro series handheld welding machine adopts an integrated design. It's unique integrated welding gun design has strong anti-return light capabilities and can continuously weld high-reflective materials without generating heat or shutting down.
Red copper itself has a large linear expansion coefficient and good thermal conductivity. Once the laser temperature is too high due to continuous welding, the workpiece is prone to deformation, which increases the difficulty of the welding work and directly affects the welding quality.
The PhotonWeld A-Pro series of handheld welders has rich welding modes. Its pulse welding mode has a maximum welding frequency of up to 50KHz . In the high-frequency welding mode, the small spot laser can penetrate copper to form a weld while minimizing the thermal impact. .
For the suppression of pores in the copper welding process, the main method is to increase the laser energy density and reduce the heat input .
PhotonWeld A-Pro series handheld welding adopts 14um "small core diameter" technology , the spot diameter is less than 40um , and the laser energy density is 300% higher than that of traditional laser welding machines. Even without wobble welding, it can effectively reduce porosity, which can be said to be a powerful tool for copper welding. In addition to reducing porosity, " small core diameter laser technology can also increase laser utilization by making the beam energy more concentrated, reduce the reflection of laser by copper, and extend the service life of lenses and handheld welders.
Lasermach continues to carry out technological innovation and research and development, continues to delve into customer scenarios, actively collects user feedback, conducts scientific research and application transformation of laser technology based on the difficulties and pain points that end users really need to solve, and uses the power of innovation and technology to create product value. Provide truly valuable solutions and establish Lasermach Laser’s own differentiated competitiveness.
Finally, if you are troubled by the problems of low welding efficiency and poor welding effect, you can contact us immediately to apply for free proofing and test machine quotas, and we will arrange senior consultants to serve you.
Laser welding with PhotonWeld A-Pro T70 a red copper tube (16x12x3mm) to a copper plate of 3mm
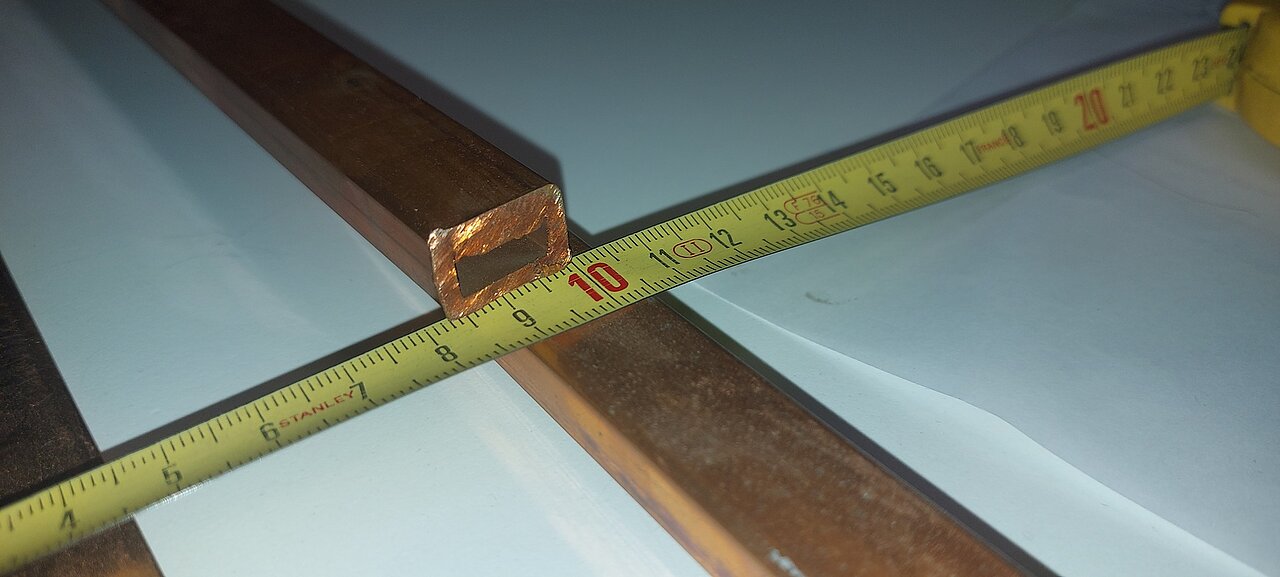
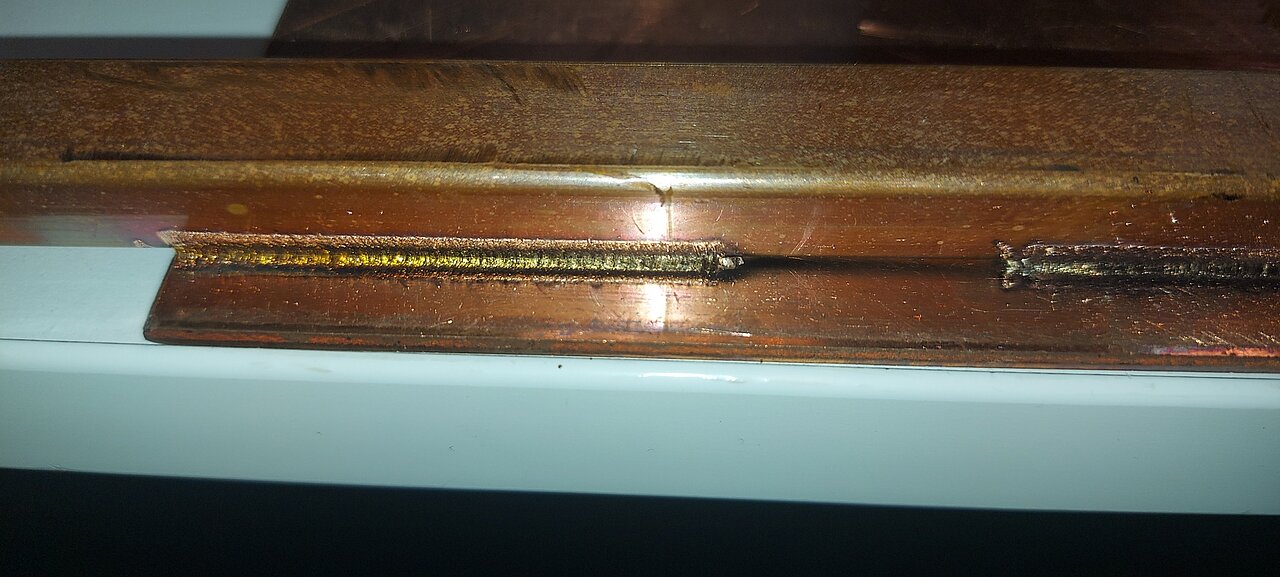
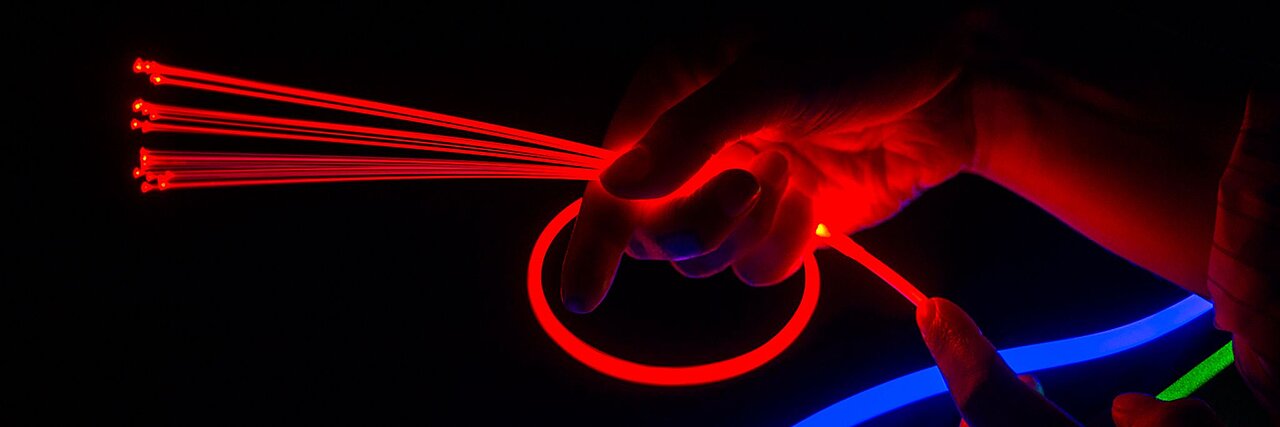
Summary
In summary, Lasermach's laser welding machines have overcome traditional challenges in copper material welding by leveraging advantages such as high energy density, precise control, and a small heat-affected zone. This has effectively addressed issues like high thermal conductivity, oxidation, and high melting points encountered in copper welding. As the demand for copper materials increases, laser processing technology is poised to become a key driving factor. Additionally, the application of green and blue light lasers opens up new possibilities for laser processing of copper materials, propelling a new round of growth in the laser industry. This development trend not only elevates the level of copper material processing but also provides reliable and efficient solutions for the modern manufacturing sector.