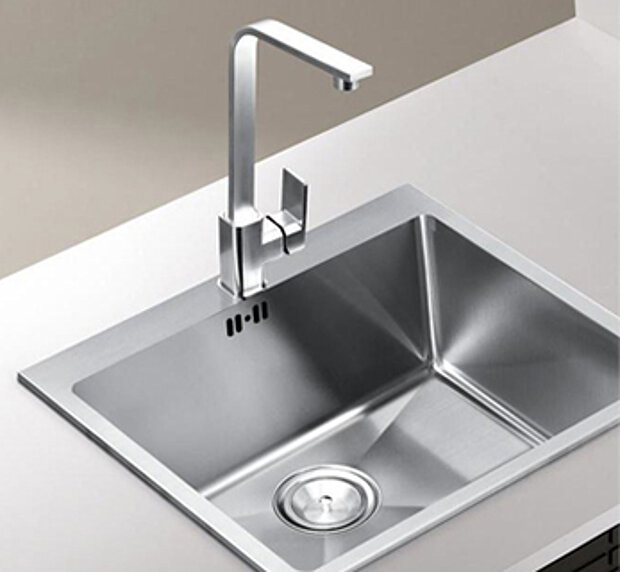
Stainless steel is an exceedingly versatile material.
It is preferred where the properties of steel and corrosion resistance are required in tandem.
Its first use was in cutlery but due to its corrosion resistance properties. Next, it found its way to the chemical industry. Today, we can see stainless steel pretty much everywhere. The use-cases vary from industry to industry.
A few industries that use stainless steel extensively:
- Food and catering
- Chemicals and pharmaceuticals
- Medical equipment manufacturing
- Architecture and construction
- Home appliances
- Offshore and shipbuilding
- Automotive manufacturing
- Energy and industry
CHALLENGE OF STAINLESS STEEL WELDING
The welding of stainless steel requires good material knowledge, because the many different alloys and steel types also have varied weld properties. The aim is to maintain the positive properties of the material even after the welding process.
INTERESTING FACTS ABOUT STAINLESS STEEL
THE PUREST FORM OF STEEL
Stainless steel is the term used for alloyed and unalloyed steels with a particularly high level of purity. The proportion of sulfur and phosphorus, the elements accompanying the iron, is below 0.025%. Stainless steel does not have to be rust-proof, but in daily life the term rust-free steel is generally only used to refer to stainless steel.
ALLOYS
The most common alloy elements in stainless steel are chromium, nickel, molybdenum, titanium, niobium, vanadium and cobalt. From a minimum content of 12% chromium, stainless steel becomes resistant. On the surface, a thin layer of chromium oxide forms due to the influence of oxygen. This protects the steel beneath it from other chemical influences.
WHAT TYPES OF STEEL ARE THERE?
A differentiation is made between several types of steel according to the components of their structure:
AUSTENITIC STEELS
These steels are also known as chrome-nickel steels (CrNi steels) and have a nickel content of more than 8%. They offer good mechanical properties, are resistant to corrosion and acid and can be processed easily. They are mainly used in aggressive environmental conditions, such as in the chemical or food industry.
FERRITIC STEELS
There are two types of ferritic steels. Their chrome content is either between 11 and 13% or around 17%. The former are only referred to as “corrosion-inert” due to their lower chrome content. They are used whenever a long service life and safety are important, while the optical appearance is less significant. Examples include container, wagon and vehicle construction.
FERRITIC AUSTENITIC STEELS (DUPLEX STEEL)
Due to having both ferrite and austenite structure components, these stainless steels are often also called duplex steels. They combine two particularly good properties: increased strength as rust-free chrome-nickel steel and increased ductility and formability as rust-free chromium steel. Due to its high resistance to surface corrosion, duplex steel is mainly used in the chemical and petrochemical industry, as well as in offshore projects.
MARTENSITIC STEELS
These stainless steels have a chrome content of 12–18% and a carbon content of over 0.1%. They can be tempered by heating and quickly cooling, and have a high strength that increases as the carbon content rises. They are used, for example, in the production of razor blades, knives and scissors. However, they are less corrosion resistant than other stainless steels.
The demand for stainless steel is annually growing at a whopping 5%.
In 2022, global production of Stainless Steel reached over 62 million tons.
At present, a wide number of industries utilise stainless steel. Aside from traditional and marine constructions, household appliances are also experiencing a rise in usage. While stainless steel is more expensive than mild steel, its excellent properties lead to increased service life and reduced cycle cost. So the larger upfront costs pay off in the longer run.
Stainless steel brings along corrosion and heat resistance besides the conventional properties of steel. It provides all the advantages of steel along with a few of its own. It does not corrode easily, endures rough environments better and has a longer service life.
But it is not completely true that it is stain-proof. Firstly, the resistance to corrosion depends on the grade. However, abnormal surrounding conditions such as low-oxygen, poor circulation and high salinity may stain it irreversibly.
Despite the above risks, stainless steel is a wonder material and has a highly positive impact on the industry as a whole. Due to so many grades with different properties, there is always a grade that is perfect for an application. It is essential to choose the grade wisely to ensure a cost-effective investment.
Laser Welding of Stainless Steel
PhotonWeld Series: Optimal solution for High speed high finish welding of stainless steels
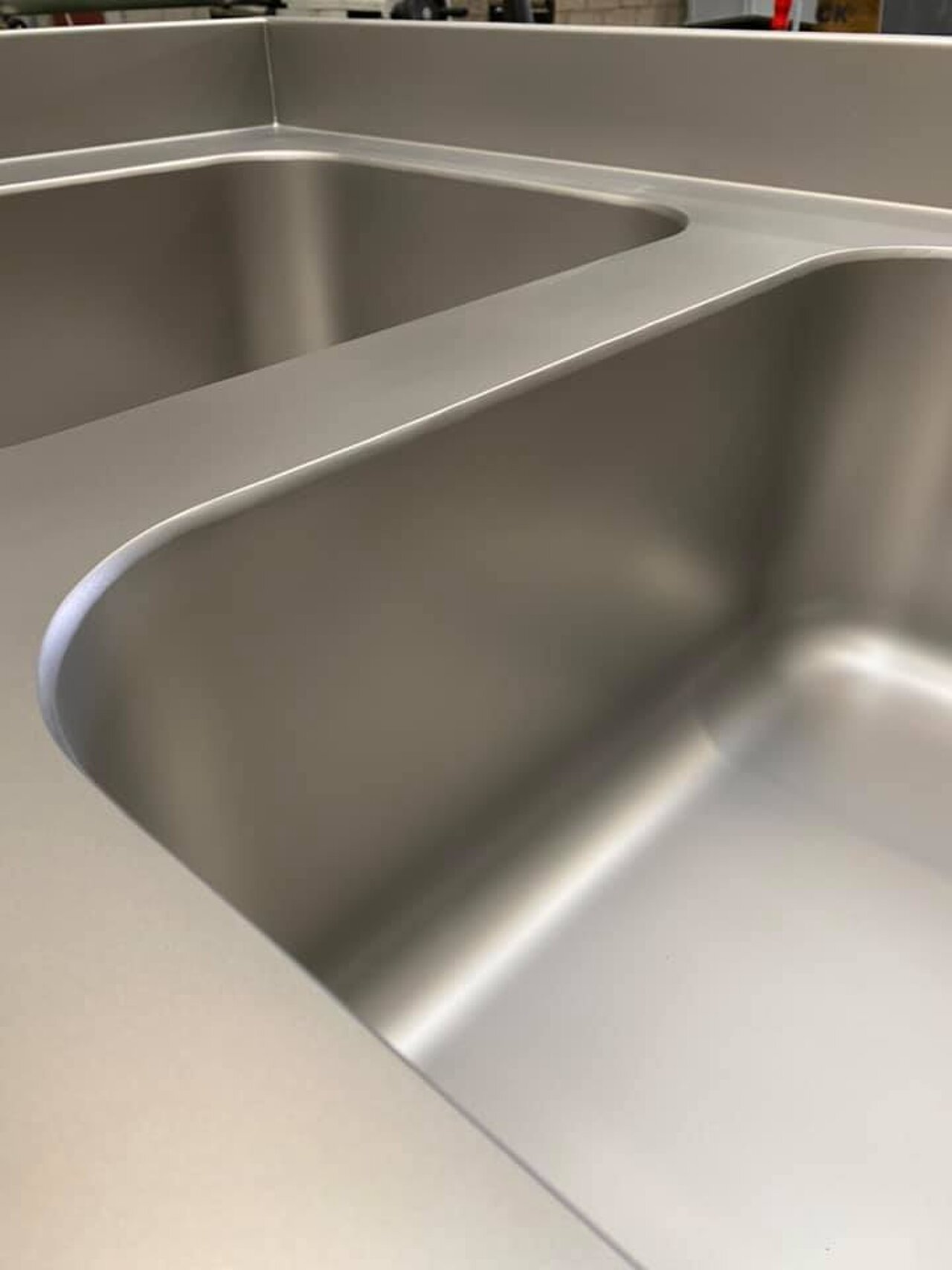
Laser welding on stainless steel: the essentials to know
Composition of stainless steels and applications
Steel is itself an alloy containing iron (minimum 50%) and carbon (between 0.02 and 2% of the total mass). By combining these two components with chromium , nickel or other elements, we obtain different steels capable of resisting oxidation. These are stainless steels or “inox”.
Each element in their composition has its own function:
- nickel ( Ni) ensures the stability and solidity of stainless steel;
- chromium (Cr), its resistance to oxidation ;
- molybdenum (Mo) offers increased resistance to oxidation in extreme conditions, particularly in highly polluted environments .
Depending on their intrinsic properties, the various stainless steels can be used in fields of activity such as the medical or pharmaceutical sector , the food industry, the chemical industry, the maritime sector, etc.
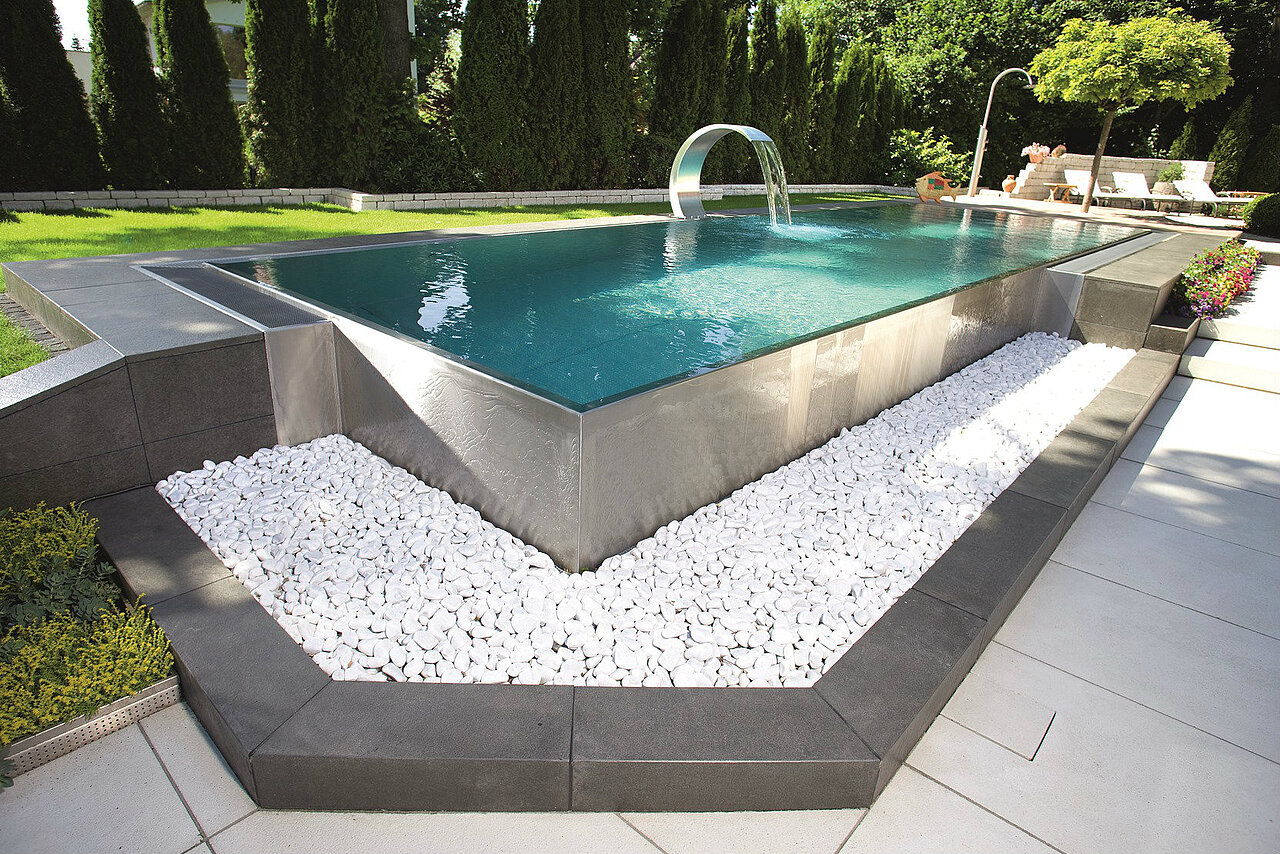
Grades of Stainless Steel
There are hundreds of grades of stainless steel in the market today. Choosing the right one for your application is important as their properties can be quite different from each other.
Types Of Stainless Steel:
There are five types of stainless steel, which are categorized based on their microstructure (microstructure in a key influencing factor in how strong the steel is going to be). Three out of the five steel types are most commonly found in fabrication shops:
- Austenitic stainless steel – the most commonly used material
- Martensitic stainless steel – used for hard facing and other high-wear applications
- Ferritic stainless steel – most commonly used for consumer products as it’s cheap to make
Each kind has it’s own benefits and difficulties when it comes to welding. The technique used to weld stainless steel is not all that different from that required to weld standard carbon steel, with two exceptions. Firstly, you must exercise more care and control with regard to heating and cooling stainless steel, and secondly, it’s more important to properly match filler metals with the material being welded.
The AISI (American Iron and Steel Institute) system for naming stainless steel is still used by the industry. The numbering system uses three-digit numbers starting with 2, 3 or 4.
200 series
This series is used for austenitic grades that contain manganese. These chromium manganese steels have a low nickel content (below 5 per cent).
200 series find use in:
- Washing machines
- Cutlery
- Food & drinks equipment
- Automotive industry
- In-doors equipment, etc.
300 series
This series is used to name austenitic stainless steels with carbon, nickel, and molybdenum as alloying elements. The addition of molybdenum improves corrosion resistance in acidic environments while nickel improves ductility.
AISI 304 and 316 are the most common grades in this series. AISI 304 is also commonly known as 18/8 steel as it contains 18% chromium and 8% nickel.
300 series stainless steel applications include:
- Food & beverage industry
- Automotive industry
- Structural for critical environments
- Medical instruments
- Jewellery, etc.
400 series
Ferritic and martensitic alloys form this series of stainless steel. These grades are available for heat treating. Providing a good combination of strength and high wear resistance. The corrosion-resistance properties are lower than 300 series, though.
Applications for 400 series include:
- Agricultural equipment
- Motor shafts
- Gas turbine parts, etc.
Preparing to Weld:
As in any type of welding, it is very important to clean stainless steel before welding it. What you may not realise, however, is how important it is to only use the tools that you use on stainless steel, on stainless steel. Tools such as brushes should be kept separate for stainless steel projects because of how sensitive the material is to the presence of any carbon steel. The same is true of stainless hammers and clamps, because trace amounts of carbon steel can become embedded in stainless steel causing it to rust.
Similarly, grinding carbon steel in proximity to stainless steel can result in the same problems. Carbon steel dust that is suspended in the air can land on stainless steel and again lead to rusting. So it’s a good idea to keep carbon steel and stainless steel work areas totally separate.
The other important factor in preparing to weld stainless steel is making sure you have the proper filler material, which means you will need to be aware of exactly which type of base material you’re welding. There are, of course, situations where it is not as simple as this, like when you are doing on overlay, or joining dissimilar metals.
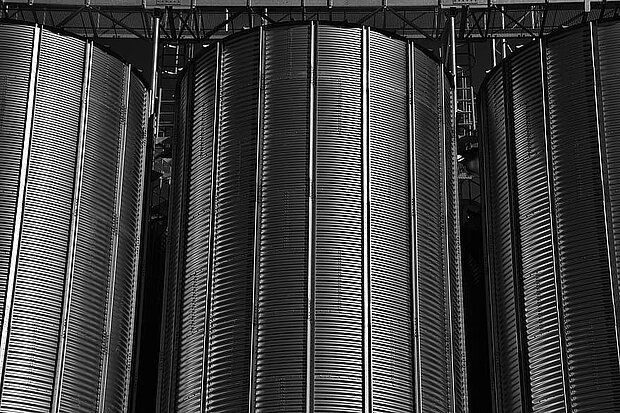
Laser welding: characteristics of the 3 main families of stainless steel
- Ferritic stainless steels: containing very little carbon, they are characterized by limited corrosion resistance and average hardness.
- Austenitic stainless steels: much richer in carbon than ferritic, they offer excellent corrosion resistance. These stainless steels (316L, 304L and 301) are frequently machined by laser welding.
- Martensitic stainless steels: able to be heat treated and hardened, they are used in the manufacture of parts where hardness is important. Hot cracking of martensitic stainless steel limits their laser machining.
Some stainless steels are magnetic. This characteristic is not trivial: magnetic stainless steel cannot be welded by electron beam. Laser welding is then the perfect solution to obtain good resistance to corrosion and chemicals, with lower costs.
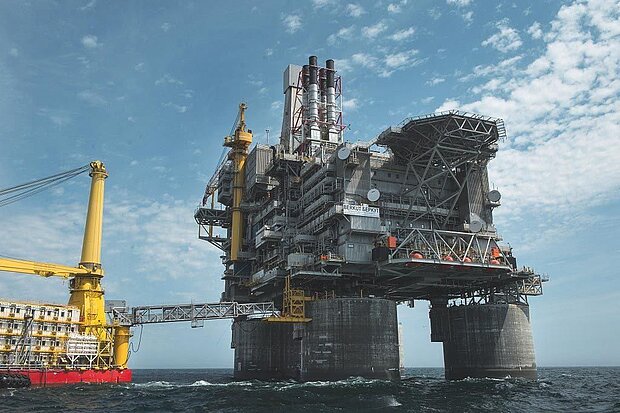
Laser Welding of Austenitic stainless steel
Austenitic steels are the most common types of stainless steel. They contain chromium and nickel as their main alloying elements. Small amounts of nitrogen are sometimes added to improve mechanical strength and pitting corrosion resistance. Superaustenitic steel is an example of an austenitic steel that has a higher alloy content, particularly with reference to molybdenum and nitrogen, than ordinary austenitic steels.
Helium, argon and argon/helium mixtures (argon/30% helium andargon/50% helium) are frequently used when working with austenitic steels. The higher the laser power, the higher the helium content that the welding gas must have in order to reduce plasma formation.
Welding gases containing hydrogen, such as argon/6–10% hydrogen,can be used at lower laser powers. Besides controlling plasma formation,hydrogen also reduces surface oxides and affects the viscosity of the melt.
Nitrogen is a suitable welding gas component for those austenitic and superaustenitic steels that are alloyed with nitrogen. Nitrogen as a welding gas compensates for loss of nitrogen in the weld metal, which would otherwise occur, thereby reducing the pitting corrosion resistance of the welds.
However, nitrogen should not be used as a welding gas for austenitic steels alloyed with titanium and niobium. Nitrogen forms nitrides with these elements, so that there is less free titanium and niobium availablefor prevention of chromium carbide formation and intercrystalline corrosion.
Laser Welding of Ferritic stainless steel
Chromium is the main alloying element of ferritic stainless steel. Inert welding gases, such as helium, argon, and argon/helium mixtures, are suitable for laser welding. Nitrogen used as a welding gas increases the nitrogen content in the melt. Therefore, nitrogen has the same effect as carbon when working with ferritic steels, i.e. it increases the quantityof martensite in the weld metal and therefore also the brittleness of the weld. Welding gases with a hydrogen content are unsuitable because ferritic stainless steels, similar to mild steels, are susceptible to hydrogen embrittlement.
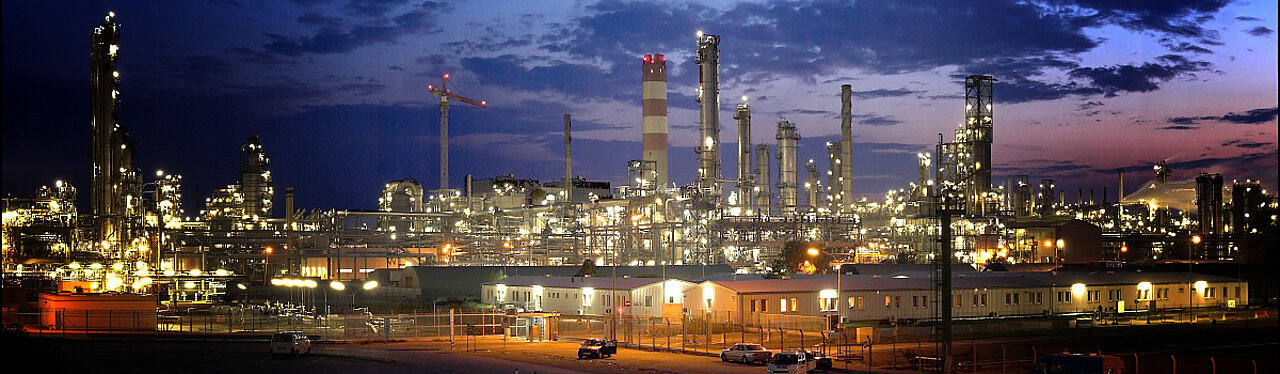
Laser Welding of Austenitic-ferritic stainless steel
Austenitic-ferritic steels are also known as duplex or super duplex stainless steels. They are characterised by a two-phase microstructure containing austenite and ferrite. As a rule, the volume fractions of austenite and ferrite are equal. The main alloying elements are chromium, nickel and molybdenum. Duplex stainless steels are usually also alloyed with small amounts of nitrogen. Super duplex steel is a higher alloyed variation of austenitic-ferritic steels.
One of the problems in welding duplex steels is that the content ofaustenite in the weld bead is reduced considerably in comparison withthe parent metal. This impairs the mechanical and corrosion properties
of the joint. Using nitrogen, argon/nitrogen mixtures, or helium/nitrogenmixtures as welding gases can increase the austenite content in the weldbead, as nitrogen absorption into the weld metal promotes the formationof austenite.
Welding gases with hydrogen content should be avoided when working with duplex steels. These materials contain significant amounts of ferrite, which is susceptible to hydrogen embrittlement.
Laser welding of stainless steels sometimes requires additional protection against oxidation of the weld and/or backing gas for the root side. As a result of the high welding speed, the hot weld metal may leave the protection zone before cooling down to an uncritical temperature and may consequently react with the ambient air. In this case, an additional gas shroud can afford extra protection for the top bead.
Argon and nitrogen/hydrogen mixtures are used as backing gases for austenitic steels. However, nitrogen/hydrogen mixtures are not recommended for titanium-stabilised austenitic steels, as there is a risk of titanium nitride formation. Hydrogen-free backing gases such as argon are recommended for ferritic steels, in order to avoid the risk of hydrogen cracking. Nitrogen is suitable as a backing gas when working with duplex steels and super duplex steels, because it generates a higher amount of austenite in the weld metal.
The importance of analysis when it comes to laser welding
Due to their tendency to crack when hot, austenitic stainless steel requires special precautions before laser assembly. For this purpose, Laser Rhône Alpes uses casting analysis tools to assess the risks of cracking of the material. Based on the chemical composition of stainless steel and their method of production, it is possible to assess the risks of cracking and recommend modifications to the material to obtain the best welding conditions .
These tests can be carried out when the quote is established or at each casting change. They meet American and European standards used in the steel industry:
- AISI (American Iron and Steel Institute): standard for naming steels according to a 3-digit reference and an optional suffix (L for Low Carbon);
- X2 CrNi 18-09 – EN 6027: equivalent European standard.