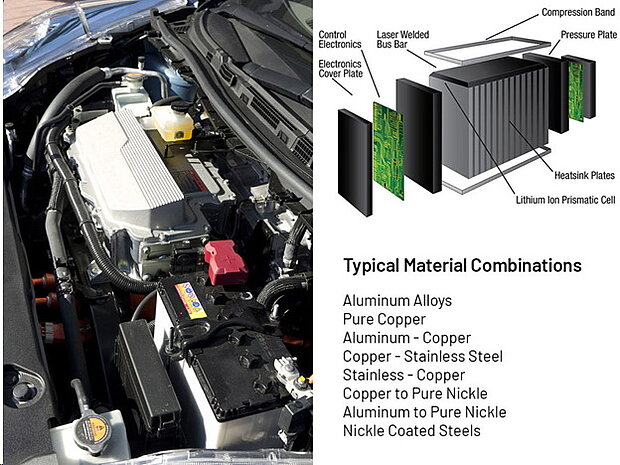
Battery Welding for EV'S
Today’s electric vehicle batteries are designed for a life exceeding 10 years.
To ensure reliable operation over this lifespan, individual components and cells within the battery are connected with numerous welds.
The increased application for lithium batteries in electric cars and many electronic devices now utilize fiber laser welding in the product design. Components carrying electric current produced from copper or aluminum alloys join terminals using fiber laser welding to connect a series of cells in the battery.
Since the battery is expected to operate reliably for 10 or more years, these laser welds are consistently high quality. The bottom line: with the correct fiber laser welding equipment and process, laser welding is proven to consistently produce high quality welds in 3000 series aluminum alloys that have connections within dissimilar metal joints.
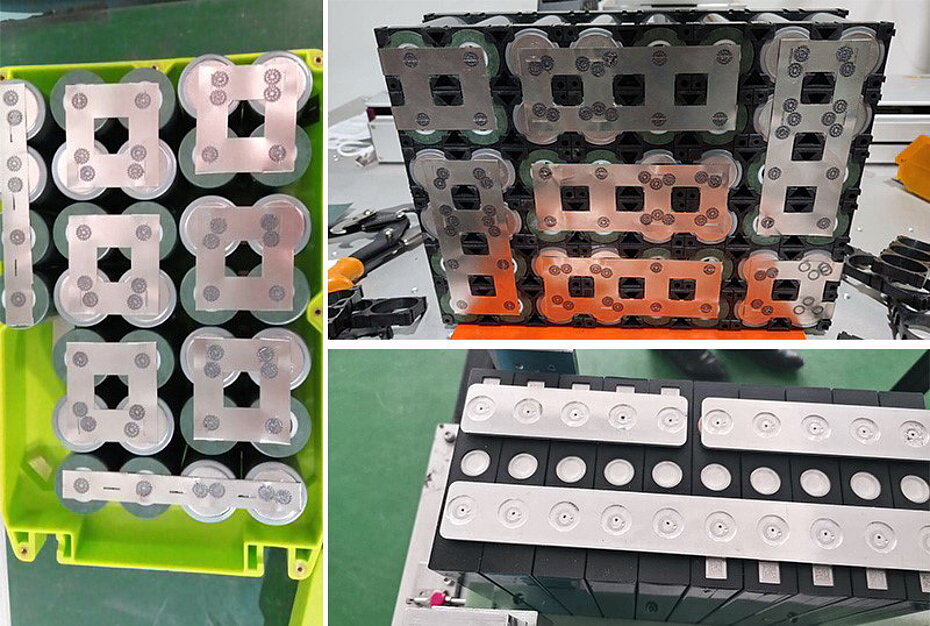
Growing EV battery market demands better joining solutions: Wobble laser Welding is the best
Laser Beam Welded Joints for Lithium-Ion Batteries
The growing electrification of vehicles and tools increases the demand for low resistance contacts. Today’s batteries for electric vehicles consist of large quantities of single battery cells to reach the desired nominal voltage and energy. Each single cell needs a contacting of its cell terminals, which raises the necessity of an automated contacting process with low joint resistances to reduce the energy loss in the cell transitions. A capable joining process suitable for highly electrically conductive materials like copper or aluminium is the laser beam welding.
Over the past years, the demand for large battery packs for electric vehicles (EV) has steadily increased with the ongoing electrification of the transportation sector and a growing demand for greater ranges. State of the art EV battery packs consist of a large quantity of cells connected in series to achieve the desired voltage level and in parallel in order to enable higher charge- and discharge-currents.
For example, the EV Tesla Model S comprises of total count of over 7000 type 18,650 battery cells inside its battery pack. A single defective connection can lead to failure or a reduction in performance.
The quality of the joint has a decisive influence on the sustainability and safety of electric vehicles: Increased resistance at a welded joint causes more heat loss at this spot and leads to an increased electrical and thermal load on the individual cells, which in turn can lead to failure or accelerated aging.
Laser beam welding is a promising technology to contact battery cells enabling automated, fast and precise production of conductive joints. In comparison to other conventional welding techniques, such as resistance spot welding, the laser beam welding has a reduced thermal energy input. Compared to ultrasonic welding, the laser beam welding technique does not induce a mechanical force. The resulting transition resistances are in the range of the basic material resistances. The overall performance of the battery pack is therefore improved by the reduction of the ohmic resistance of the joints and heat loss inside the battery cell.
High currents must flow through the welds between battery cells in order to deliver the electricity needed to power a battery electric vehicle. These welds are the bottleneck of the electric circuit. Electrical resistance causes the temperature in the welds to raise when a current is conducted. This temperature increase may be harmful to lithium-ion battery cells. Therefore, larger weld areas which are created with our wobble laser system, and thus lower resistance. Thewelds made by wobble welding system increase the mechanical strength of the welds drastic, and reduce the temperature and thermal stress at the joints. Considering this, Wobble Laser Welding is much more suitable for battery tab joining than other types of welding.
Furthermore, laser beam welding produces a small heat-affected zone. Hence, it is crucial to understand how much heat is generated in the weld and whether the heat can damage the battery. Lithium-ion batteries must operate within a safe and reliable operating area, which is restricted by temperature and voltage windows. Exceeding the restrictions of these windows will lead to rapid attenuation of battery performance and even result in safety problems.
In the context of production, laser beam welding is well suited to be integrated into almost fully automated production lines in the manufacturing process of battery packs and EVs.
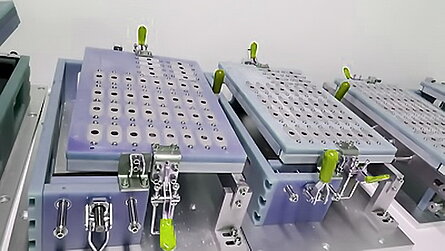
Laser Wobble Welding – Flexible Weld dimensions
As laser welding has no limitation on the proximity of the welds, the laser can place any pattern of weld spots on the tab or with the wobbling technology the wobble laser can weeld any diameter of circle according to strength requirements. If the weld strength of the joint is achieved, conductivity follows.
For more conductive materials, the weld area required for strength can be as much as 10 times that required for conduction. Although peel strength remains an important weld test, vibration is also important. As vibration strength places an emphasis on having good weld strength in any direction, the circle weld of wobble welding provides the solution.
Laser Welding in Lithium-ion Battery Manufacturing
The battery industry adopted conventional machinery for processing before laser technology put into use. Compared with traditional machining, laser processing machine has the advantages of flexible cutting and/or welding shape, better finishing quality, higher accuracy and lower operating costs, which is conductive to reduce manufacturing costs, improve production efficiency, and significantly shorten new product’s die cutting cycle.
As the core components of new energy vehicles, lithium battery directly determines the performance of vehicle. With the gradual outbreak of new energy vehicle market, laser cutting and/or welding machine will own great market potential in the future.
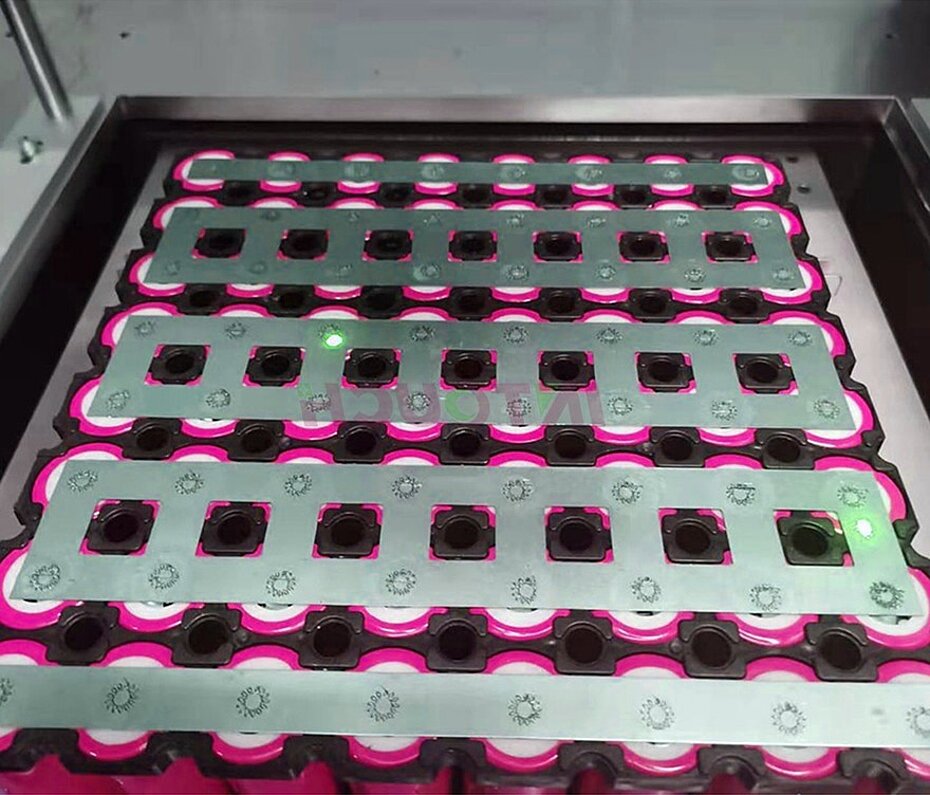
Bonding session of EV battery packs
A battery pack in an EV consists of a large number of individual battery cells that are held together mechanically and connected electrically. Making those mechanical and electrical connections poses several challenges, including the joining of multiple thin, highly conductive materials of varying thicknesses and potential damage through thermal or mechanical shock.
These factors drive the range of techniques for constructing a battery pack, from resistive and ultrasonic welding to micro arc welders, highpower lasers and even high magnetic fields.
The choice also varies with the type of cell, whether it be cylindrical, pouch or prismatic. The different cell types have different mechanical requirements, but they all need to be protected against high temperatures during the construction process.
Materials challenges in the production of EV battery-packs
A battery pack has to use different materials, and this creates a challenge for joining dissimilar materials. It can create brittle intermetallic layers with higher electrical resistance and a brittle nature compared with the parent materials. Highly reflective surfaces can be a challenge for processes such as laser welding, while surface coatings or oxide layers can be a challenge for resistive or ultrasonic bonding.
The joint strength is of course vital, and a stronger bond takes longer to create with many techniques. However, the bonding has to be created with minimal vibration that can be transferred into the cells – a key challenge for ultrasonic systems and a big advance fort laser Welding.
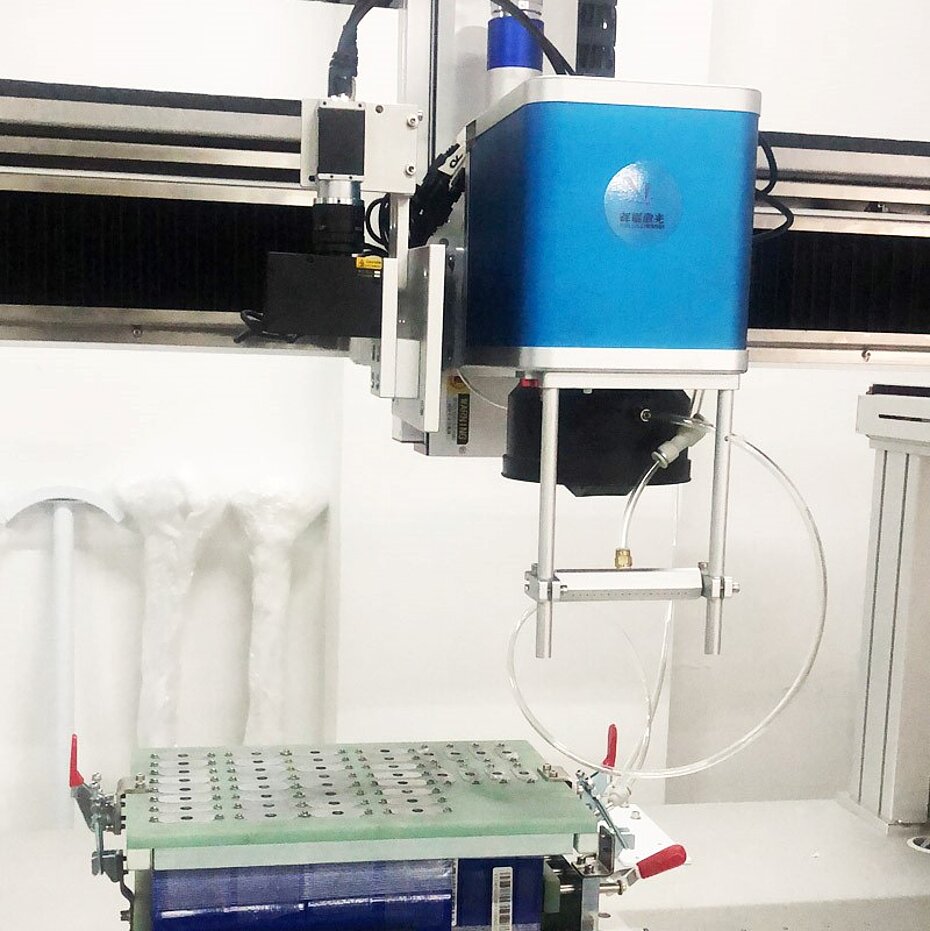
Using Lasers for Battery Tab Welding Applications
Battery Tabs Welding with laser
From a welding perspective, the most important aspects of tab welding are the thickness and material of both the tab and the terminal. Conductivity is the name of the game, so battery tabs are generally made of aluminum or copper, sometimes plated with nickel or tin. Terminals may be cold rolled steel, aluminum, or copper, depending upon the physical size of the finished battery.
The most common battery types are cylindrical lithium ion cells around the 18650 size (18 mm x 65 mm), large prismatic cells, and lithium polymer pouch cells. Each cell type has a different set of welding requirements.
Cylindrical batteries
The key to welding the cylindrical cell type lies in the negative terminal weld, where the battery tab is welded directly to the can as opposed to the separate platform on the positive side. The weld on the negative terminal must not penetrate the can thickness which is typically around 0.3mm. The thickness of the can dictates how thick the tab can be – a rule of thumb is that the tab should be 50-60 % that of the can. Cylindrical battery can material is usually nickel-plated steel, and the tab material nickel or tin-coated copper. Nickel plating is preferred over tin because it is more stable; tin’s very low boiling point can lead to weld porosity and excessive spatter.
Large prismatic batteries
These high capacity cells need thick tabs to ensure a sufficient current carrying cross-section to deliver the pack output. However, the tab connection needs only to deal with the capacity of a single cell. Therefore, thinning or “coining” of the thick tab material to enable a lap weld or creating a through hole for a fillet weld greatly reduces the size of the weld needed. This in turn reduces heat input to the can, which is always a concern when welding thicker tabs.
For a lap weld geometry, reducing the tab thickness to a 0.25-0.5 mm thickness enables sufficient weld area for strength and capacity while keeping the temperature during the weld low enough to avoid battery damage. Material selection is generally aluminum for both terminal and tab – recommended tab materials are 1080 and 1100. Avoid aluminum alloy 6061, which cracks when welded. If this material is already specified and cannot be changed, use a 4047 pre-form as a third material which will introduce a large amount of silicon into the weld, which prevents weld cracking.
Lithium polymer batteries
These pouch type cells, which are thin with a rectangular footprint, are really gaining traction for consumer electronics. The terminals on these batteries are made up of thin layers of copper and aluminum foil which are laser welded to tab of copper and aluminum respectively. This weld is traditionally made using ultrasonic technology due to the need to weld through a stack of foil, however, fiber laser welders are now being used for increased weld quality and strength.
The key to success in welding polymer batteries with a fiber laser is making sure that the foils are in close contact and you’re using a pulsed laser or even better a wobbling laser to avoid overheating.
Welding battery Tabs to battery Terminals
From a welding perspective, the important aspects of tab welding are the thickness and material of both the tab and the terminal.
Resistance welding is suited to welding nickel tab material up to 0.4 mm thickness, and nickel or steel clad copper tab material to around 0.3 mm thickness to a wide variety of terminal materials.
Laser welding is able to weld both thin and thick tab materials, with a capability of welding copper based or bi-metal tab material above and beyond 1.5 mm thickness
Although able to weld both thin and thick tab materials, laser welding is particularly well suited to addressing the needs of high power battery welding. The tab material used in the development of high power cells must be able to accommodate the associated higher capacities and power levels. In order to provide effcient energy transfer, a tab thickness of minimum 0.3 mm or greater is required, as is the use of more conductive materials. For high power lithium ion cells, the terminal material for certain battery manufacturers is different. Therefore the need for bi-metal and smart terminal design solutions is required. Defining the optimal tab material may require some development work both on the welding and material costing. In these cases, the laser is an invaluable tool that offers outstanding welding performance and flexibility.
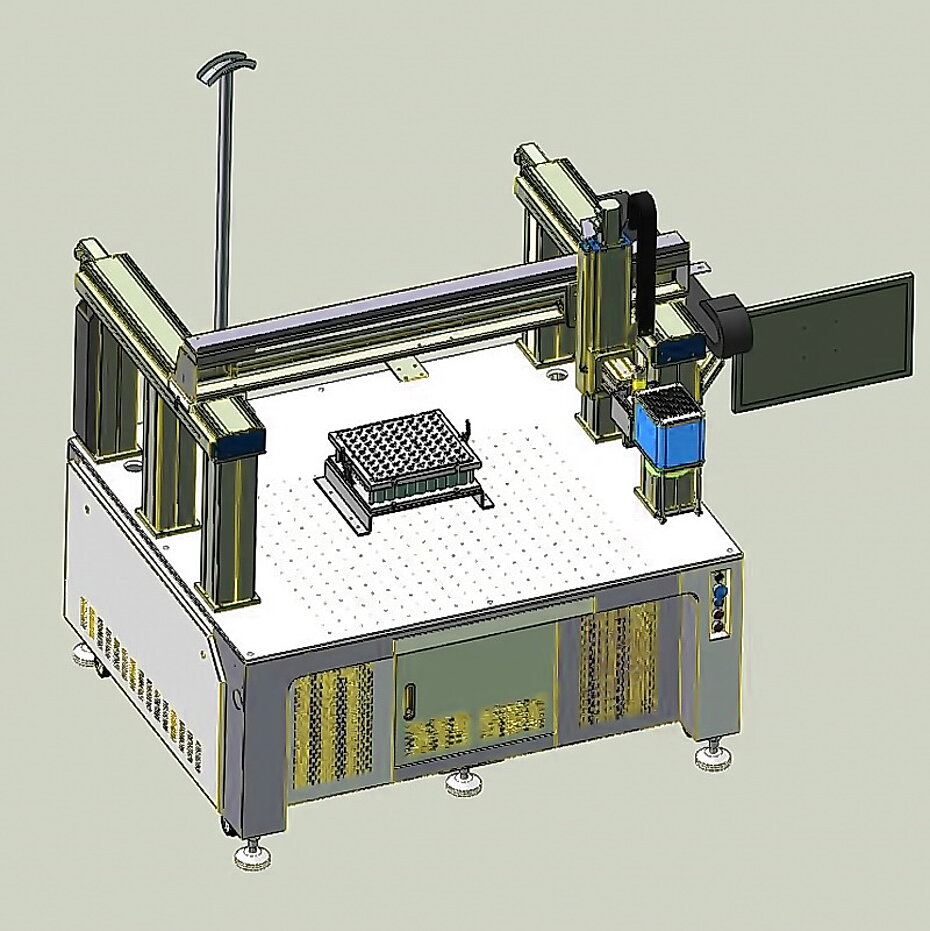
Battery Pack Manufacturing Solutions
When planning an automated or semi automated solution based on our Wobble cube, the primary factors to consider are loading/unloading, motion and tooling that fit the planned production flow and production rate.
Loading and unloading can range from manual to conveyer or pick-and-place, motion options center around whether the laser head or the part will be moved, with options including XYZ tables and gantry’s or robotic manipulators. For tooling, the laser is non contact, so tooling of the parts can be achieved either by using a fixture that the batteries and tabs are loaded into, or using actuated tooling that is deployed prior to the welding process.
The most suitable technology and process for battery pack manufacture relates to a number of factors including the pack size, thickness and material of the tab itself, and the necessary production rate. Laser welding processes enable high quality volume production, and, of the two joining technologies today used, spot welding and laser welding, the selection is usually made based on the specific requirements in each situation, but laser welding is taking over very fast from the spot welding, especially with the excelent wobble laser welding technology.
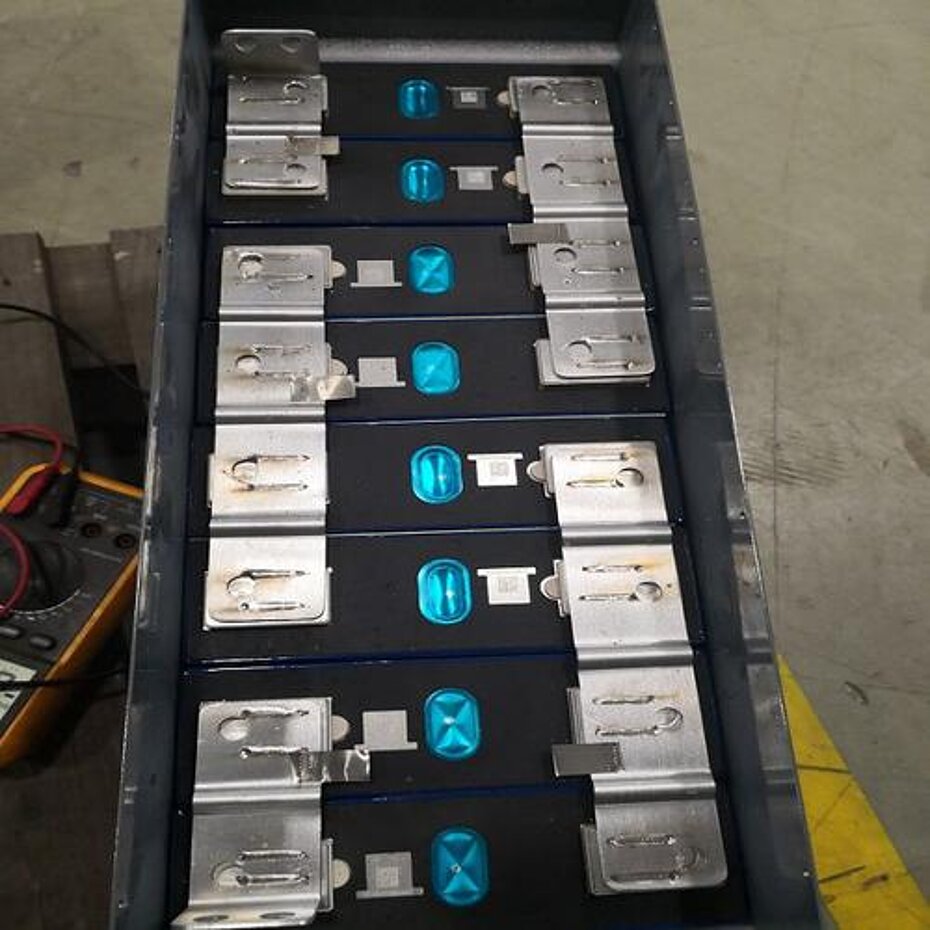
High efficiency lithium battery tabs laser welding machine
1. Welding of battery explosion-proof valve
The explosion-proof valve of the battery is a thin-walled valve body on the battery sealing plate. When the internal pressure of the battery exceeds the specified value, the valve body of the explosion-proof valve ruptures to prevent the battery from bursting. The safety valve has an ingenious structure, and this process requires extremely strict laser welding technology. Continuous laser welding can achieve high-speed and high-quality welding, and welding stability, welding efficiency and yield can be guaranteed.
2. Welding of battery tabs
The tabs are usually divided into three materials. The positive electrode of the battery uses aluminum material, and the negative electrode uses nickel material or copper nickel-plated material. In the manufacturing process of power batteries, one of the steps is to weld the battery tabs and poles together. In the production of the secondary battery, it needs to be welded with another aluminum safety valve. Welding must not only ensure the reliable connection between the tab and the pole, but also requires a smooth and beautiful weld.
3. Spot welding of battery poles
The materials used for the battery poles include pure aluminum tape, nickel tape, aluminum-nickel composite tape, and a small amount of copper tape. The welding of battery electrode strips generally uses pulse welding machines. Due to its good beam quality and small welding spot, Modulated CW lasers or QCW quasi-continuous lasers are suitable for high reflectivity aluminum strips, copper strips and narrow-band battery strips (polar strip width (Under 1.5mm) welding has unique advantages.
4. The power battery shell and the cover plate are sealed and welded
The shell materials of the power battery are aluminum alloy and stainless steel (stainless and acid-resistant steel). Among them, aluminum alloy is mostly used, generally 3003 aluminum alloy, and a few use pure aluminum. Stainless steel is a laser weldable material, especially 304 stainless steel, whether it is pulsed or continuous laser, it can obtain welds with good appearance and performance.
5. Power battery module and pack welding
The series and parallel connections between power batteries are generally completed by welding the connecting piece and the single battery. The positive and negative electrodes are made of different materials. Generally, there are two kinds of materials: copper and aluminum. Ultrasonic welding was usually used before, but its being replaced by laserwelding due to the regulary mechanical damage in the battery resulting from the ultrasonic vibrations. Copper and copper, aluminum and aluminum are generally used. Using laser welding. Both copper and aluminum conduct heat very quickly and have a very high reflectivity to the laser. The relatively large thickness of the connecting piece requires a higher power laser welding.
Applications fields for E-mobility
Battery Cell/Module Electric Drive/Powertrain Power Electronics Battery Pack/Battery Frame Can-Cap welding Tab welding Bus-bar welding Slitting of foil Cutting of foil Welding of foil Cleaning, ablation and drilling of foils Hairpin stripping/decoating Hairpin welding Welding of cast housing Wire welding of differential Cutting, cleaning and ablation of surfaces DCB welding Welding of external contacts Welding of housing Cutting, cleaning and ablation Beyond E-mobility: Advanced Driver Assistance Systems Cutting of frame/ case material Welding of case Consulting/support: Layout design and construction of frame/case for battery pack Laser cleaning