Application of Laser Welding Machine for Door and Window Industry
Customisable & Affordable & Reliable production of steel windows
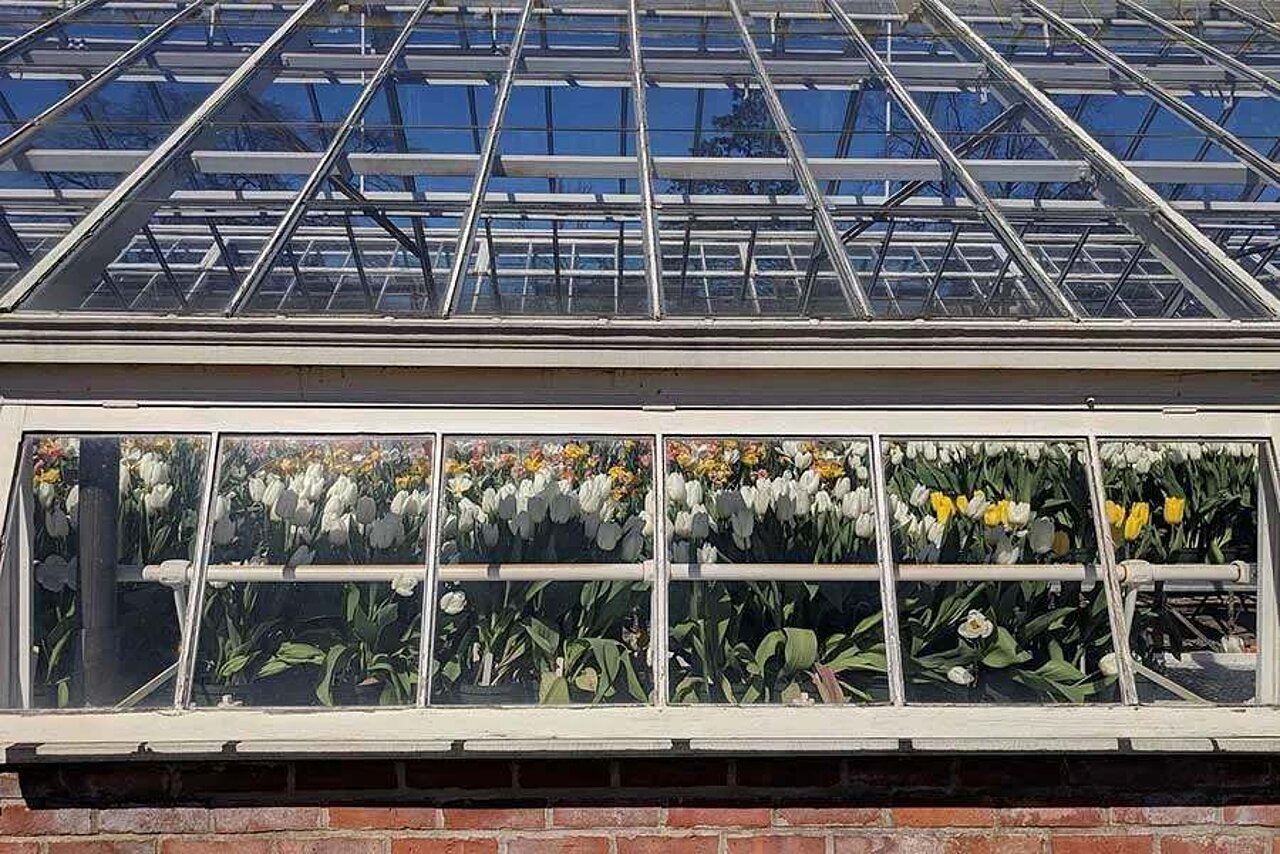
Hand-held laser welding machine for windows and doors production
With industrial development and the implementation of energy-saving policies, the production scale of environmental protection windows and doors such as aluminium alloy and stainless steel has gradually expanded. The problems of rising material and labour costs, low processing efficiency and uncontrollable quality are particularly prominent in the production and installation of windows and doors.
Nowadays, it is very common for laser welding aluminium alloy or stainless steel windows and doors. Compared with the traditional welding processes, laser welding machines have the characteristics of various functions, uniform light energy, and beautiful welding seam. During the welding process, wire feeding welding can be used to reduce welding problems such as pores, cracks, and depressions, effectively enhance the absorption rate, and avoid damage to the substrate. The laser welding machine is very popular in the windows and doors market, it is not only easy to operate, but also finely processed, which greatly improves the sealing, wind resistance and pressure resistance of windows and doors.
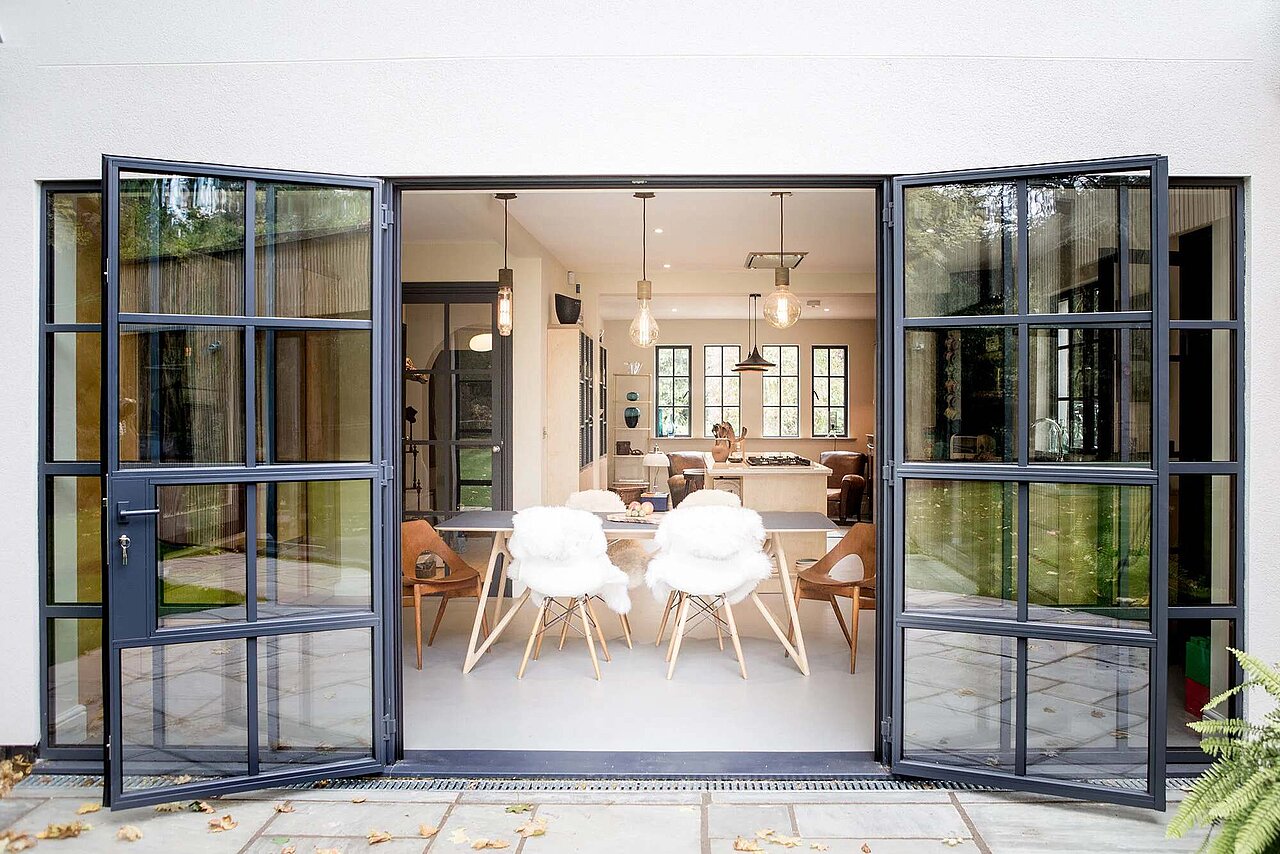
Laser-welded aluminium, steel or stainless steel windows and doors have fine processing, beautiful and consistent welding spots, strong sealing and durability.
In generally, customers will choose and buy windows and doors products that have both aesthetics and quality. And the windows and doors processed by the hand-held laser welding machine can achieve this effect, which is more in line with the customer's choice.
- Beautiful appearance : The aluminium or stainless steel material is processed by hand-held laser welding machine, and the surface is flat and free of concave and convex. Through further grinding and spraying, can achieve the seamless connection effect. At the same time, in the process of laser welding, qualified shielding gas will be used to keep the welding seam and the base material consistent.
- Long service life : With Laser welded windows and doors, the weld metal and the base metal are perfectly integrated, the weld is very firm, smooth, and has good sealing performance, which can effectively solve the problem of water seepage caused by the traditional glue injection process and long-term use, achieve comprehensive protection and increase the service life of windows and doors.
- Processing safety : PhotonWeld hand-held laser welding machine is equipped with a safety control system, the output power is stable, and there is no slag splashing during the welding process. In addition, wearing safety helmets and protective glasses can more effectively ensure the safety of operators.
During the processing of the hand-held laser welding machine, it is usually necessary to weld the corners of the windows and doors.
Laser-welded aluminium, steel or stainless steel windows and doors have fine processing, beautiful and consistent welding spots, strong sealing and durability. The use of hand-held laser welding machine can effectively improve the overall performance of windows and doors products, and also make manufacturers stand out from many peers. PhotonWeld A-Pro is the best choice for enterprises to improve production efficiency and quality.
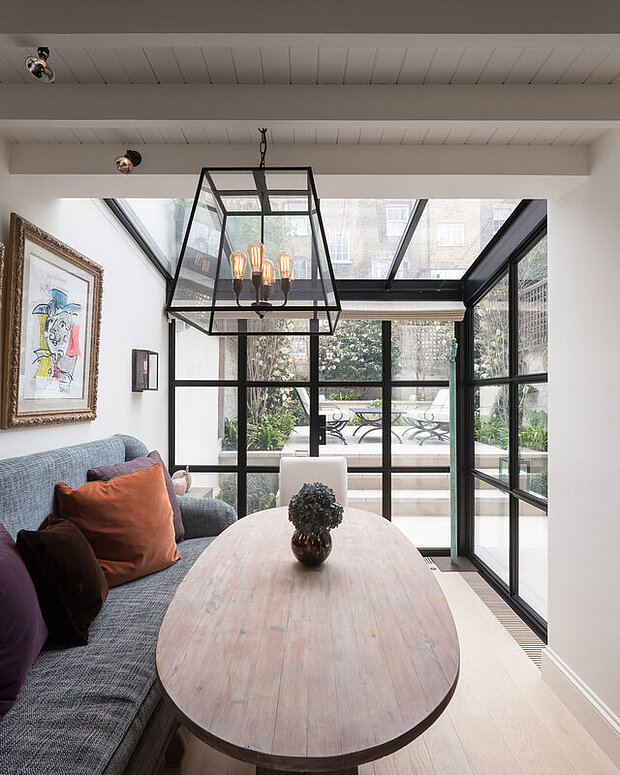
Laser Welding for Windows and Doors
Precautions for Laser Welding Aluminum Alloy Windows
Laser welding technology produces smooth, attractive weld seams with no welding scars, work-piece deformation, or weak joints, thus reducing the need for post-weld grinding and saving time and costs.
- High-speed welding for labour and time savings: Laser welding operates at speeds 2-10 times faster than traditional methods, requiring no extensive training and reducing the need for multiple welders.
- Flexibility for multi-angle welding: The handheld welding gun allows for welding work-piece at various angles, offering exceptional freedom of operation in any position.
- Space-saving versatility in welding: Without the need for welding tables, it occupies minimal space and can be used for a wide range of welding products, accommodating various work-piece shapes.
- Cost-effective welding choice: With low energy consumption and minimal maintenance costs, laser welding provides an economically viable welding solution.
- Aesthetic weld finishes, reducing post-processing
Precautions for Laser Welding Aluminium Alloy Windows
Because aluminium alloy is a non-ferrous metal with strong reflectivity to various types of light, laser, being an even more intense beam of light, can cause even more pronounced reflections on its surface. Aluminium alloy also possesses high thermal conductivity. Therefore, when aluminum alloys laser welding, it is crucial to swiftly increase the power density of the laser to prevent reflection or conduction.
Aluminium materials have characteristics of high thermal conductivity and reflectivity. Thus, welding parameters must be chosen according to the specific type and thickness of the aluminium material. Selecting appropriate power, focal length, and focus diameter parameters allows for control of the heat input and the formation of the molten pool during welding, ensuring the desired weld appearance and quality.
Attention must be paid to factors such as beam quality and gas shielding to guarantee welding quality and stability.
- Pre-weld cleaning: Before welding, it is essential to thoroughly remove any oxidation, rust, and oil residues from the welding joint and wire surface of aluminum alloy doors and windows. This can be achieved through chemical, mechanical, or laser cleaning.
- Backing plate: Due to the low strength of aluminium alloy at high temperatures, the welded joint metal is prone to collapse during welding. Backing plates are used to support the molten pool and nearby metal, preventing collapse.
- Alignment: Precise positioning and clamping of door and window components is necessary to ensure they do not move during the welding.
- Pre-heating: When welding aluminium alloy doors and windows with a thickness typically ranging from 10mm to 15mm, pre-weld heating is required. Different types of aluminum alloys have varying melting points and thermal conductivities, so pre-heating temperatures usually fall between 100°C to 200°C.
- Post-welding steps: Allow for a cooling period to reduce heat stress
Weld seam cleaning: Remove any remaining welding slag and oxides from the weld seam and its surrounding area. Passivation treatment: To enhance the corrosion resistance of aluminium alloy doors and windows, consider surface treatment or coatings on the weld seams.
Thermal Barrier
Laser welding of window profiles with thermal barrier
Tradition and innovation
Steel windows today are manufactured using sections with old traditional design. This evolution of the steel sections allows the windows to be double-glazed with thermally efficient units, helping contribute to a stringent BFRC ‘B’ energy rating.
Traditional single glazed steel windows can still be manufactured using the standard metal window range of steel profiles. These window profiles are the basis of the ‘standard window’ that is installed in many homes throughout the world.
Hot rolled profiles for steel windows
Steel windows have been, and still are, the preferred choice of architects, especially when their function is not to close a hole in a wall but to make a significant contribution to the character and overall appearance of a façade.
The minimalist aesthetics of hot rolled steel sections and their ability to shape windows is unique. Their slender lines appear to lose weight and give lightness to the frames, emphasizing the transparency of a façade.
New regulations force to new solutions
This elegance is difficult to match in the bulky profiles of alternative materials like PVC, aluminum or wood. Unfortunately, due to the lack of a thermal insulation, these “historical” windows made from hot rolled steel sections have become an endangered species and with it the architectural window design and culture of a century.
Future regulations on thermal insulation ask for a new generation of hot rolled steel sections, which not only replace and preserve the character of national heritage buildings, but also give architects the possibility to use windows with distinguishing visual qualities that bring back the beauty in contemporary architecture.
For the last 25 years, the design of windows was driven more by regulations to increase thermal performance, rather than by their original scope, which is the contribution to enhance the beauty of buildings. This technological run for better insulation of window frames forced manufacturers to introduce thermal brakes in metal systems or to look for alternative materials like PVC, which have better insulation characteristics by nature.
Lately new thermal barrier steel window system, which combines the essence of the original steel window design of the last century with state-of-the-art manufacturing technology have become available.
The outer profiles are made from cold formed steel, which is joined by a cast in polyurethane. The section’s geometry reproduces the thin and slim shape of the traditional style window sections reaching highest thermal insulation levels.
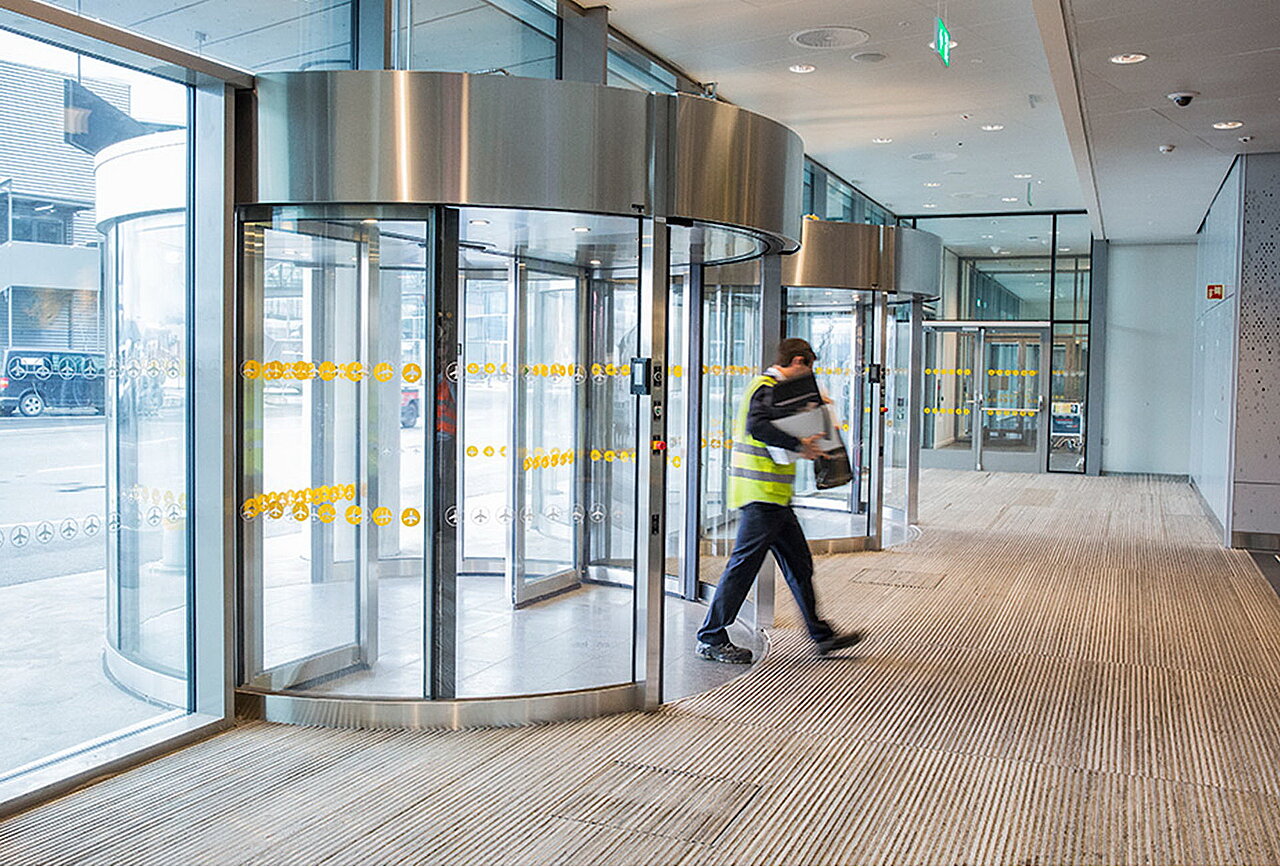
Low Impact Laser Welding for windows and doors construction
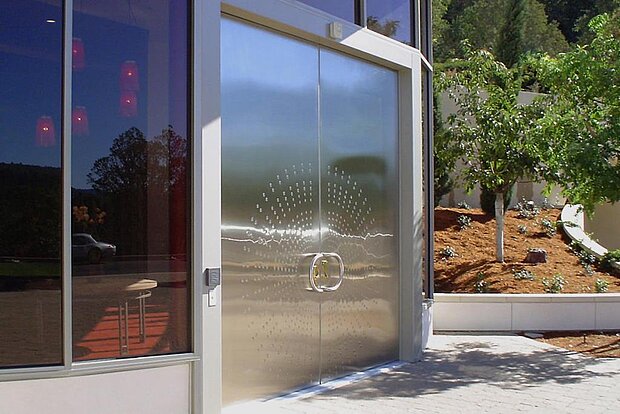
Laser welding in the door and window industry
The application of laser welding machine in the door and window industry, with high degree of automation, can not only achieve high efficiency, good operation, good welding effect, etc., but also significantly reduce labor costs and enhance product compet
The application of laser welding machine in the door and window industry, with high degree of automation, can not only achieve high efficiency, good operation, good welding effect, etc., but also significantly reduce labor costs and enhance product competitiveness.
Laser welding equipment processing often only needs to adjust the welding parameters according to the thickness of the aluminium alloy doors and windows. The welding process does not require the addition of welding wire and other auxiliary consumables. For stainless steel products, such as stainless steel doors and windows, handrails and stainless steel craft products, the welding required laser power is smaller and easier to weld.
The uniform energy distribution of the welding spot ensures the beauty and performance of the welded work-piece. Laser welding machine with multi-beam processing, can realize the mass production, and show the advantage of high output ratio in the same series of products.
Compared to traditional welding processes, laser welding machines are highly functional, highly reliable, do not require vacuum conditions and are highly efficient. It has the advantages of high power density, low total heat input, large depth of melt with the same heat input, small heat affected zone, small welding deformation, high speed, and easy industrial automation.
Traditional processes require the use of sheet metal stacks for welding, while laser welding machines do not require contact with the surface of the processed item throughout the process, so the laser process has advantages that traditional welding methods cannot match.
Laser applications are very broad. Laser welding machine as a direction of laser application is based on the synthesis of traditional processing technology and modern laser technology. Due to the shortcomings of traditional welded window and door processing, laser welding has gradually replaced traditional processing methods.
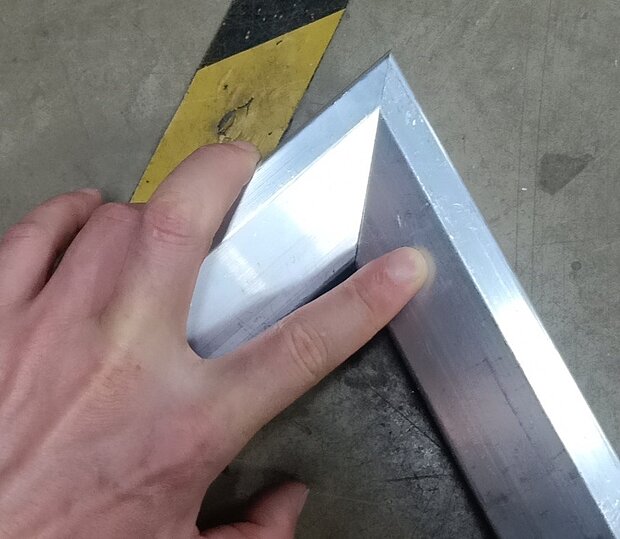
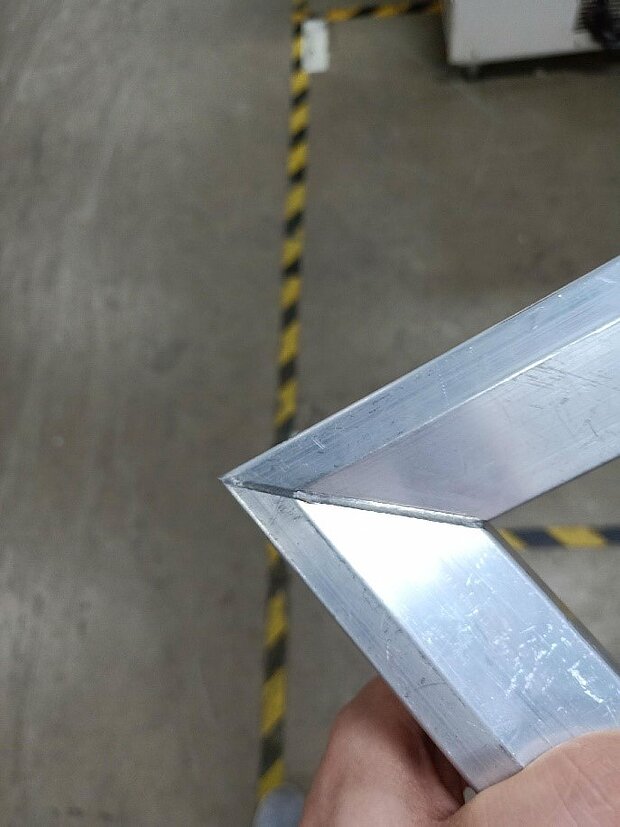
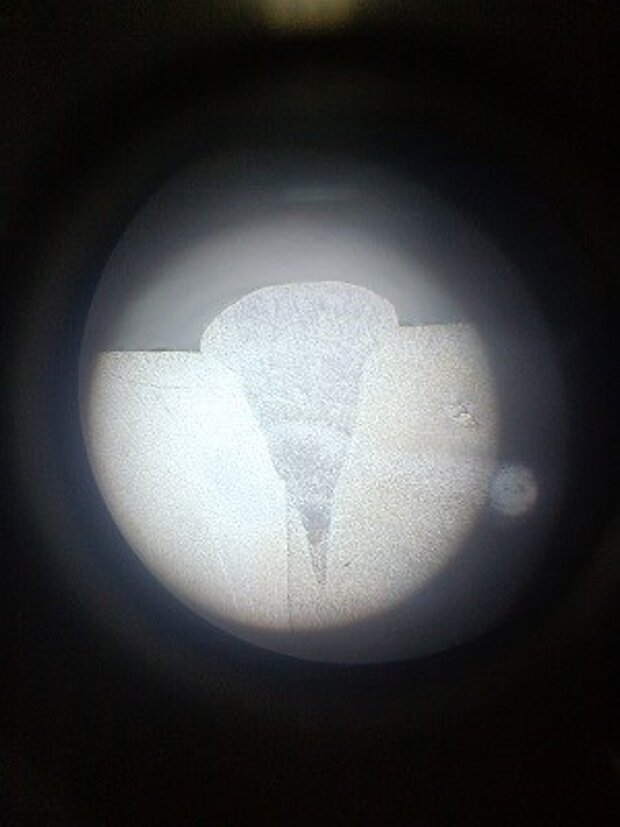
WELDED METAL WINDOWS VS. MECHANICALLY-FASTENED: WHAT’S THE COMPARISON?
Comparison: a Typical Mechanically Fastened Assembly System VS. Dynamic’s Laser Welded Construction
A key feature of Steel, Bronze or Aluminium series of thermally broken metal windows and doors is that components are cut, welded, ground smooth, and then painted. This results in a different product than a mechanically-fastened system.
MECHANICALLY-FASTENED METAL WINDOWS
The standard method of assembling aluminum or steel systems typically involves mechanically-fastened profiles, either nailed, screwed, or crimped together. It’s a quick and efficient way to manufacture, requiring fewer fabrication process steps. Finishing costs are much lower with fastened systems. Profiles are painted in long linear lengths then cut and assembled. Finishing in linear lengths results in faster finishing times and improved transfer efficiency (material loss) than assembled frames.
Mechanical fastening is the industry’s standard method of assembling aluminum or steel window systems.
Why would you want to seriously consider welded construction?
Comparison: a Typical Mechanically Fastened Assembly System VS. Dynamic’s Laser Welded Construction
WHY WELDED CONSTRUCTION MATTERS: STRENGTH, AESTHETICS AND DURABILITY
Laser welded construction is extremely strong.
Strength, aesthetics, cut lines and enhanced protection against corrosion.
Lines – there are none!
When profiles are mechanically-fastened, you’ll see the corner connections/mitre cut lines at every profile intersection. They are visible enough that they become, in effect, a part of “the look”. If the profiles do not align perfectly (keeping in mind that metal moves constantly under expansion and contraction) and depending on the color, shadow lines will occur or exposed shiny aluminum at the cut edges – particularly noticeable on dark finishes. With welded construction that is ground to a smooth finish, there are no exposed mitred cuts, the result is a clean, seamless finish – an aesthetic associated with steel windows.
Enhanced protection against corrosion.
When mechanically fastened, the mitre cuts expose the raw aluminum of the profiles. If mitred end cuts are not factory sealed with a liquid guard or similar sealer, the exposed aluminum can oxidize and creep under the paint, causing potential paint failure (peeling, flaking etc.). This is why mechanically fastened aluminum fabricators recommend edge guard protection if the project is within 3 miles of the ocean or some similar criteria. If the system is ordered without edge protection and is within a specified distance from the ocean there can be a warranty compliance conflict so it’s worth being sure. Read the fine print.
If you’re going to consider a mechanically-fastened system, ensure the supplier includes a protective coating at the mitre joints. In some cases, it can be a substantial cost increase as it adds an additional complexity to a normally expedited production system – a bit like stopping the printing press in full flow because someone wants one newspaper with the font in pink. The pink ink doesn’t cost much but the disruption to a volume-oriented production line is substantial.
With a welded system, by definition, there are no exposed mitre joints. This eliminates corrosion at the connections, thus there is no substantial cost increase to use a protective coating. You don’t need one.
TECHNICAL BENEFITS SUMMARY
Welded construction systems will always cost more than a clip-together mechanically-fastened system. It’s the nature of the beast. There is all the added labor of detailed welding and grinding to get those surfaces seamless and perfect.
Welded frames are also painted once assembled. This costs substantially more than finishing the linear lengths used in mechanical systems as you’re finishing and moving large components, not bars of profiles. As an example, if a linear profile costs $20 to finish, an assembled frame will cost $100 to finish. You get what you pay for, but you do pay more.
Welded construction as a standard will have enhanced corrosion protection with no exposed mitred joints. Mechanically-fastened systems have exposed aluminum edges as a standard, and they can seal those edges at substantial cost to the project budget. Ensure you speak with your aluminum window supplier about sealing options and the resulting cost. The nature of welded construction means all joints are removed with complete paint coverage as a standard.
ARCHITECTURAL AESTHETICS SUMMARY
With a thermally broken narrow aluminum profile that is laser welded, ground smooth and then finished, you achieve an aesthetic on par with steel windows but at a lower price point than steel – which is the reason we designed the Alumin-Arte system in the first place. It is not intended to compete on price with a mechanically fastened aluminum system – it won’t. It is intended to offer a steel aesthetic when a) steel is over budget b) the project is ocean front and steel isn’t the appropriate material to specify (including stainless) and/or c) both of the above.