
The simplest solution for your challenges: Cobot Laser Welding.
Fast, flexible, and economical welding automation for medium-sized enterprises.
Collaborative robot welding, or Cobot welding in short, is an ideal system for automating small and medium-sized series.
Why?
First, the assisting robot does not need to be enclosed in a protective cell. Welders can interact with the Cobot directly.
Second, the amount to be invested into Cobot welding is significantly lower than that for far less flexible industrial robot welding.
Cobot welding will help you master the challenges faced by medium-sized businesses.

Lasermach Cobot Welding Tool
More than 23% of commercial welding in the United States an Europe is done by a robot or a Cobot! A percentage that will rapidly grow as fabricators look for ways to streamline production. Collaborative robots (cobots) make automation a cost-effective proposition even for small shops.
Small or medium shops generally don’t have the consistently high volume necessary to justify a complex robot welding cell,
Collaborative robots (cobots) allow fabricators to gain the benefits of automation without an industrial robot’s large footprint or high price tag. Because they don’t require programming language expertise, they’re relatively easy to learn and deploy – making them cost-effective for lower-volume production runs with a higher mix of part sizes and design features. As a result, they’re crucial to alleviating the impact of fewer skilled welders entering the trade.
Nor are they intended to replace human welders. Instead, they automate dirty, dangerous, and dull welding-related tasks so their human counterparts can enhance a shop’s capabilities – and profitability – by producing more complex work.
Add Flexibility Without Sacrificing Safety
As the need for automation grows, smaller shops are asking for solutions that fill the void in the overall robot market for welding.
To meet this need, we developed a 3 compact and adaptable robotic solution that safely and effectively works alongside skilled welders and production employees. Unlike traditional robots, the cart fits through a standard doorway and can run on lower voltage power so it can be moved and operated virtually anywhere.
Easy to Learn
No prior robot experience is required! User-friendly interface and plug-and-play features allow for an effortless cobot welding experience.
Weld any Metal
With the fibre laser power unit, it is possible to perform welding on various types of metals such as steel, stainless steel and aluminium.
Increase Productivity
PhotonWeld Combi C-Series work tirelessly, increasing production efficiency, ensuring maximum output and reducing manual labour requirements.
Decrease Costs
By utilizing cobot welders, material waste can be minimized and the need for rework can be reduced, resulting in significant cost savings while ensuring precise and consistent welds.
Improved Safety
Advanced sensors and collision detection technology make CoboMate safe to work alongside human employees.
Welder Shortage
PhotonWeld C-Series combi laser welding cells, helps solve the skilled labour shortages in the industry by automating repetitive and demanding tasks.
Future Proof
Investing in cobotic welders positions manufacturers to stay competitive and adapt to the evolving demands of the industry.
Local Support
Our team of experts is offering our services across the nations. We are extending our dealer and distribution netwerk every day to give more service nearby.
We are just one phone call away: +32(0)56333240
C-Series Collaborative Laser Welding Robots
A partner you can rely on in production
The C-series features a cabinet-free design with a built-in torque sensor in every joint, leading the market in deployment flexibility, safety, and ease of use, extending its applicability to healthcare, commercial use, new retail, and more.
Widely and deeply involved in the Laser Welding industries, PhotonWeld C-Series raises production efficiency and lowers costs for enterprises, injecting continuous innovations to metal welding industries with its innovative, highly efficient, and competitive comprehensive intelligent manufacturing solutions.
Compensating for a lack of skilled workers.
- Greater productivity through simple operation and high flexibility
- Efficient and reliable achievement of the required production quantity
- Time and physical relief for skilled workers: Welders programme the welding task and operators perform it with the Cobot
Ensuring quality, reducing costs.
- Constant and reproducible welding quality – 365 days a year
- Great quality of results leading to less rework and less scrap
- Clear cost savings thanks to reliable high quality
- Safety and health conditions drastic increased for operators
Staying at the pulse of the time.
- A simple step towards Industry 4.0
- High renown as an attractive, future-oriented, and ergonomic employer
- Investment costs pay off quickly by very High ROI.
- Ecological responsable investment
- Big savings by greater roduction in quantity and quality

A World of Laser Welding Possibilities
Pre-Engineered Cobotic Laser Welding Cells - PhotonWeld-R COBOT TurnKey Automation Solutions
Lasermach's cobotic laser welding systems are pre-engineered, pre-assembled and shipped ready to weld - delivering the most flexible and cost-effective options to integrate cobotics into your welding processes. PhotonCube® can be configured with multiple cobots, a heavy-duty positioner or servo-controlled external axes for coordinated motion.

Collaborative robots (cobots) make automation a cost-effective proposition even for small shops.
More than 20% of commercial welding in Europe and in the United States is done by a robot, a percentage that will grow as fabricators look for ways to streamline production.
Industrial welding robots help their human coworkers move parts, handle material, palettize, assemble, torque, and by bringing parts to the welder. While they work well for large-scale applications that can afford to buy a robot designed to perform just one task, small shops generally don’t have the consistently high volume necessary to justify a welding cell that must also be fenced or otherwise safeguarded to protect employees from injury.
Collaborative robots (cobots) allow fabricators to reap the benefits of automation without an industrial robot’s large footprint or price tag. Because they don’t require programming language expertise, they’re relatively easy to learn and deploy – making them cost-effective for lower-volume production runs with a higher mix of part sizes and design features. As a result, they’re crucial to alleviating the impact of fewer skilled welders entering the trade.
Cobots consume less floor space than an industrial robotic welding cell. Their smaller footprint provides greater flexibility and more opportunities to automate tasks. Nor are they intended to replace human welders. Instead, they automate dirty, dangerous, and dull welding-related tasks so their human counterparts can enhance a shop’s capabilities – and profitability – by producing more complex work.
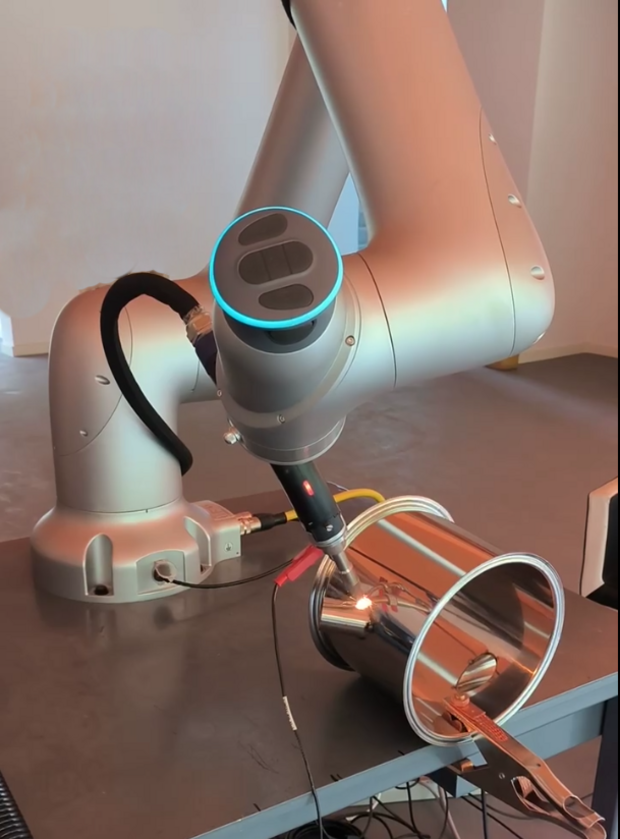
Cobotic Welding Cells
Cobotic laser welding cells are confined cubicles designed to contain the welding cobots so the arms can move freely and navigate around easily without the risk of damaging other components or harming the operators by the dangerous laser beam.
The welding cell includes metallic barriers, weld cobot, and components required for the cobot to operate, such as the laser welding torch, power supply, robotic positioners, and other welding fixtures. It will also have laser beam shields, light curtains, laser scanners, and other safety equipment. The advantage of these features of cobotic welding cells is that —
- The flexible cobotic arm can reach and weld in difficult spaces and complex geometries
- The cell barrier will protect the operators from unwanted glare and splatter
- The cells equipped with proper ventilation hoods efficiently extract the hazardous fumes
- The cobotic arm can be extended to move within the well-engineered cell layout, so it does not interfere with other equipment or manual workspaces
In addition to these operational advantages, the increasing adaptation of weld cobots and cobotic laser welding cells also means the following —
- The automated laser weld cobot runs at a set speed and process parameters during each pass, producing consistent, uniform, and high-quality results.
- The predictable performance of the cobot makes it easy to take on the attainable job and precisely deliver, especially when the demands fluctuate.
- The automated cobotic system enhances productivity for manufacturers during the welder shortage.
Weld cobots can produce repeatable results at a consistent speed with less waste, unlike manual welding, improving the cost efficiency of the process.
Getting Started with Cobot Laser Welding
Robotic laser welding applications open up a whole range of opportunities for companies of all shapes and sizes. Compact, lightweight, and quickly redeployed with relative ease, cobots are designed to fit around existing production equipment and processes. With the right solution from Photonweld, our laser cobot welder can bring immediate positive impact on manufacturing operations.
Robotic Welding with Cobots? For Sure! Absolutely!
Cobots are growing in all applications of robotic welding.
In 2023, cobot laser welding systems hit the market. Laser welding allows for better control, reducing distortion, deformation, undercutting and burn through on thin materials. It is also significantly faster than TIG welding, which really challenges even experienced welders. The precise path control of the cobot enables the fastest cycle times. Cobot laser welding cells also benefit from the introduction of small handheld laser welders, bringing down total systems cost to a level that supports payback of 1 year or less.
Cobot laser welding is a type of welding that combines the precision of a laser beam with the flexibility and ease of use of a collaborative robot, also known as a cobot. The cobot is programmed to move the laser welding head along the weld path, while the laser beam provides the heat required to fuse the materials together. Cobot laser welding is particularly well-suited to welding small to medium-sized parts with high precision, such as those used in the medical or aerospace industries. The cobot can easily be programmed to adjust the position of the laser welding head to accommodate for different part geometries and sizes, making it a highly flexible solution for a range of welding applications.
One of the advantages of PhotonWeld laser welding is that it is a highly repeatable process, which reduces the risk of defects and ensures consistent quality across production runs. The technology also offers a high degree of control over the welding process, allowing for adjustments to be made in real-time to ensure the desired results are achieved. Another advantage of cobot laser welding is that it is a low-heat input process, which minimizes the risk of material distortion and cracking. This makes it a useful technology for welding thin materials, where traditional welding methods may cause warping or deformation.
Overall, PhotonWeld laser welding offers a range of benefits, including high precision, flexibility, and ease of use. With its ability to deliver consistent quality and high repeatability, cobot laser welding is an attractive solution for manufacturers looking to improve their welding processes and increase productivity.

The Future of Cobot Laser Welding: Innovations Shaping Tomorrow's Manufacturing
One of the most exciting developments in recent years has been the rise of robot welding and collaborative robot welding, or "cobot welding."
These intelligent Laser Welding cobots are transforming the welding industry, offering unprecedented flexibility, precision, and efficiency. As we look ahead, the future of cobot laser welding promises to be even more remarkable, with advancements poised to reshape the way we weld and build.
In the dynamic landscape of manufacturing, innovation never stands still. Here are some of the trends we think will change and enhance cobot welding:
1. Advanced Sensing and Vision Systems: One of the driving forces behind the future of cobot welding is the continuous improvement in sensing and vision technologies. Tomorrow's cobots will be equipped with advanced sensors and vision systems that can perceive their environment with greater accuracy. This means improved seam tracking, weld inspection, and adaptive welding techniques, ensuring consistently high-quality welds.
2. Enhanced Precision and Control: The future cobot welders will offer unprecedented levels of precision and control. With improved path planning algorithms and real-time adjustments, cobots will navigate complex weld paths with ease, resulting in welds that meet the most stringent industry standards.
3. Collaboration with Humans: As safety standards and technology evolve, cobots will increasingly work alongside human welders, creating synergistic partnerships. This collaboration between humans and cobots will maximize productivity and efficiency while ensuring safety in the workplace.
4. Customization and Flexibility: Manufacturers will demand more versatile cobot welding systems, capable of handling a wide range of welding processes, materials, and product configurations. Future cobots will be highly customizable to meet specific industry and application needs.
5. Data-Driven Insights: Cobot welding systems of the future will be IoT-enabled, allowing for data collection and analysis during the welding process. This data-driven approach will enable predictive maintenance, process optimization, and real-time quality control, leading to improved efficiency and reduced downtime.
6. Sustainability and Efficiency: Environmental concerns are driving the development of more energy-efficient cobot welding systems. These systems will consume less electricity, aligning with sustainable manufacturing practices.
7. Cost-Efficiency and Accessibility: As cobot technology matures and competition increases, the cost of cobot welding systems is likely to decrease. This will make these innovative solutions more accessible to a wider range of businesses, including small and medium-sized enterprises.
8. Global Expansion: The global market for cobot welding solutions will continue to expand as more industries recognize the benefits of automation in welding processes. Companies looking to stay competitive will increasingly turn to cobot welding to improve productivity and quality.
The future of cobot welding is bright, marked by advancements in technology, safety, and applications. As we embrace these innovations, we're set to revolutionize the welding industry, making it more efficient, sustainable, and adaptable to the ever-changing demands of modern manufacturing. Whether you're in the automotive, aerospace, or construction industry, the future of cobot welding holds promise for all sectors.
Stay tuned as we continue to explore the exciting developments and trends in the world of cobot welding, where innovation knows no bounds.
The incorporation of cobots in the welding industry represents a groundbreaking transformation. At Lasermach, our team is dedicated to supporting you in embracing this cobot revolution and guiding you through your initial step into the world of cobotic laser welding.
Contact us today to learn more about our laser welding and laser cleaning systems!