Produce MUCH More with the Fabricators you Already Have !
Fabrication Cobot and Robot Solutions Made for Welders
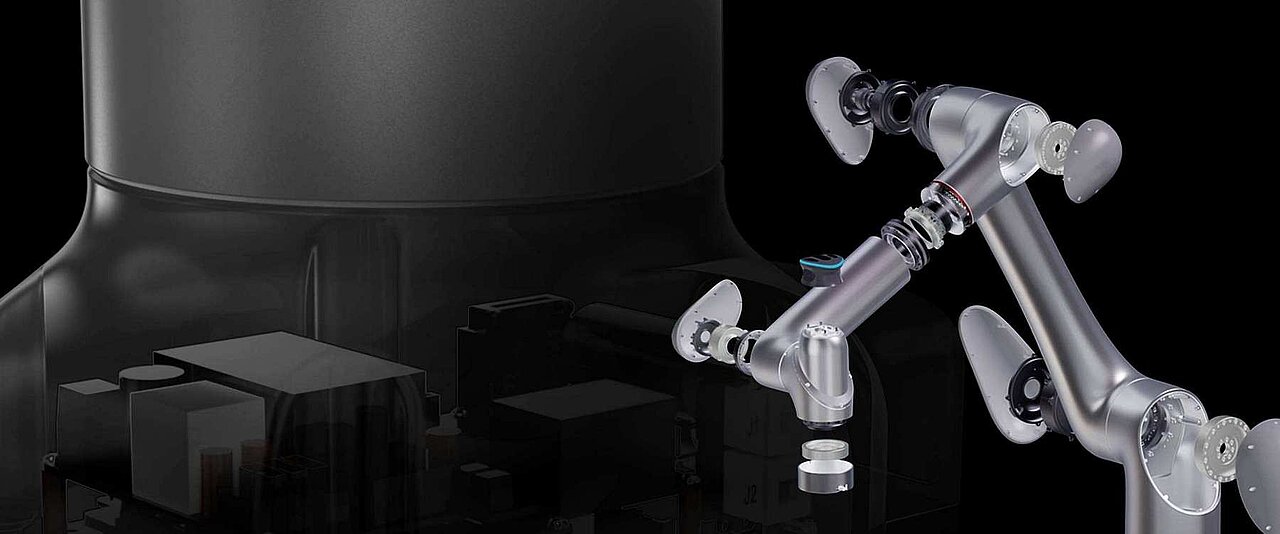
Unleashing the Power of Cobotic and Robotic Laser Welding:
Laser Efficiency, Robotic Precision, Cobotic Safety and Unmatched Quality
Accessible Automated Laser Welding
Boost productivity and get consistent weld quality with an automated laser welding tool
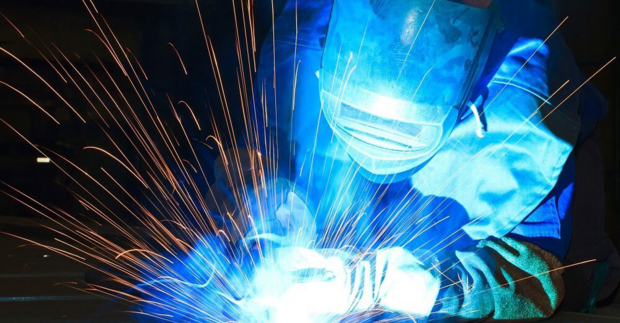
Struggling with welder shortage?
- Struggling to find and retain skilled welders to meet your current production demands?
- Do you struggle with decreased output and a sluggish time to market?
- Do you have backlogs or lose contracts because you can't produce more?
Most traditional automation cells are not suited for your high-mix and low-volume production needs and need you to hire programmers which doesn't solve your initial problem: a lack of qualified labour. Empower your welders to work on high-value tasks and let the Cobot laser Welder increase drastically your Business Productivity and Quality
One of the biggest requirements for manual TIG welding is the need for an experienced welder. TIG welding is in itself a very clean process, but it requires high consistency. This is one of the biggest benefits of switching to robotic TIG welding or even better to robot Laser welding. The upfront cost of adding a collaborative robot is significantly less than an industrial robot and also provides quick ROI as it can help increase the welding productivity in a shop. This is the case with Lasermach's Laser welding cell, which the company notes is the first of its kind for Laser Welding welding.
Automated Laser welding is something you don’t hear much about yet in the industry – especially in comparison to automated MIG welding – but interest is growing. For many fabrication shops performing on a daily base a lot of welding, the switch from manual to automation is a promising option. For these shops, it’s helpful to understand the pros and cons involved in automatic Laser Welding, with the pros definitely outweighing the cons.
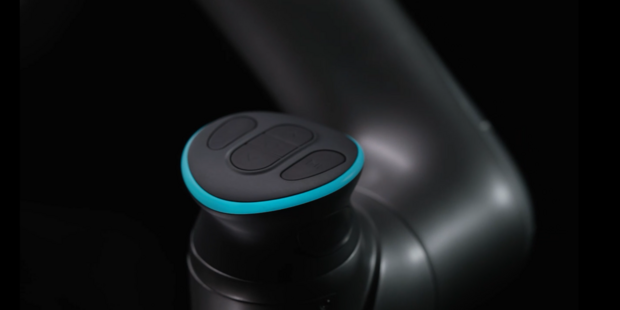
Fast to Production
Faster time-to-teach makes automated welding of smaller batches affordable and efficient.
Our welding cobot tool includes proprietary technologies, like the smart teaching puck and the smartphone application, making it hands down the fastest laser welding cobot to set up and teach on the market.
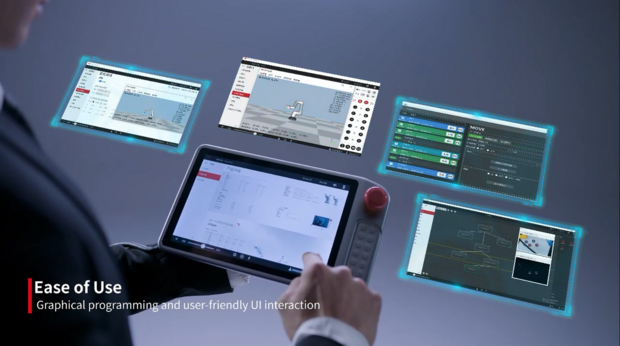
Empower the Welders you Already Have
Your productivity hinges on ease-of-use for your welders, not robot programmers. Welders care about torch angles and weld settings, not formulas and coordinate systems. Empowering your welders to program the cobot laser welding tool by themselves is good for technology adoption and your bottom line.
Cobot or Robot: which one to choose?
You can consider following 5 factors to know which type of robot can help you the most in your application :
1. Industrial requirements :
As a plant manager, you have goals and KPIs to reach to make your business sustainable. Those should be the first things in your mind when making your buying decision.
The first requirement is about performance and cycle time.
On an equal footing, industrial robots provide unmatched technical specifications against collaborative robots. They are often faster, more accurate, powerful, and reach further. They thus better improve your cycle times and throughput rate. But collaborative robot models are providing higher and higher performance.
The second requirement is production volume and part variation.
Industrial robots are made to perform in high-volume manufacturing processes with low variations. They are not easy to reprogram and redeploy on new cell settings and part configurations.
Cobots, on the other hand, can flexibly adapt to part variations. You can set different programs for your different kinds of parts, and deliberately switch from one to the other. You can also place your cobot on a mobile platform to move it from one cell to another. So cobots are a perfect fit for high-mix, low-volume manufacturing processes.
Another requirement is the size, weight, and location of your parts.
Industrial robots are made to lift and handle heavy and large parts, which can be sometimes hard to reach. Meanwhile, collaborative robots thrive with low and medium part specifications and depend on their respective reach capabilities.
2. Type of application :
Industrial robots are still the best options when it comes to material removal and assembly applications, while collaborative robots show impressive results in finishing, machine tending, pick and place, and quality control applications.
Depending on your application, choose wisely which type performs the best.
3. Work settings
Do you have a huge manufacturing floor, or can you allocate only a small working cell to your robot? As they need fences for safety reasons, industrial robots can take up a lot of space. In contrast, collaborative robots safely work alongside your employees, so they can save you a lot of space and facilitate your worker’s movements.
4. Human resources
Do you have automation-expert engineers, or are you short of programming talents? That might greatly matter, as collaborative robots don’t need specific qualifications to code them, while industrial robots require more technical skills.
5. Automation goal :
What’s your main goal? Improving throughput, cycle time, turnaround time, freeing up workers from tedious tasks, improving their safety on the floor, maximizing output quality, or minimizing waste…?
All-in-all, collaborative robots can improve your worker experience while providing greater performance and quality. Industrial robots exclusively aim at augmenting your speed and quantity of output. Your final decision will depend on what you want to improve on your manufacturing line.
You now have everything in your hands to make a mindful decision. Cobot or robot, it’s all up to you!
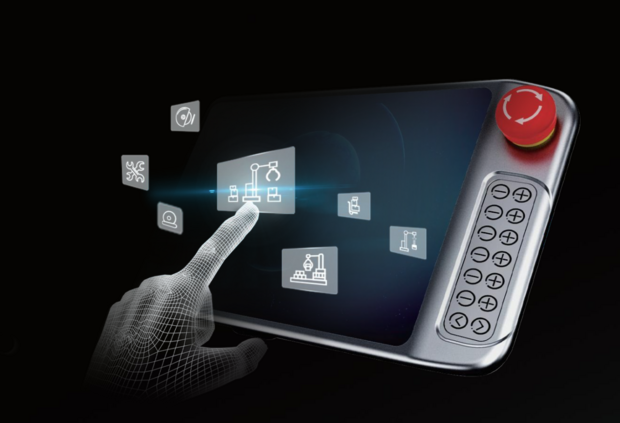
Industry-First Laser Welding Cobot Programmed with Your Phone or Tablet
Welding has never been this simple.
Ditch the robotic jargon, complexities, and even the robot teach pendant. Our intuitive app allows your welder to teach the Cobot Laser Welder without programming knowledge.
They simply enter the welding parameters and teach the welds with both hands on the robot, thanks to our Smart Puck.
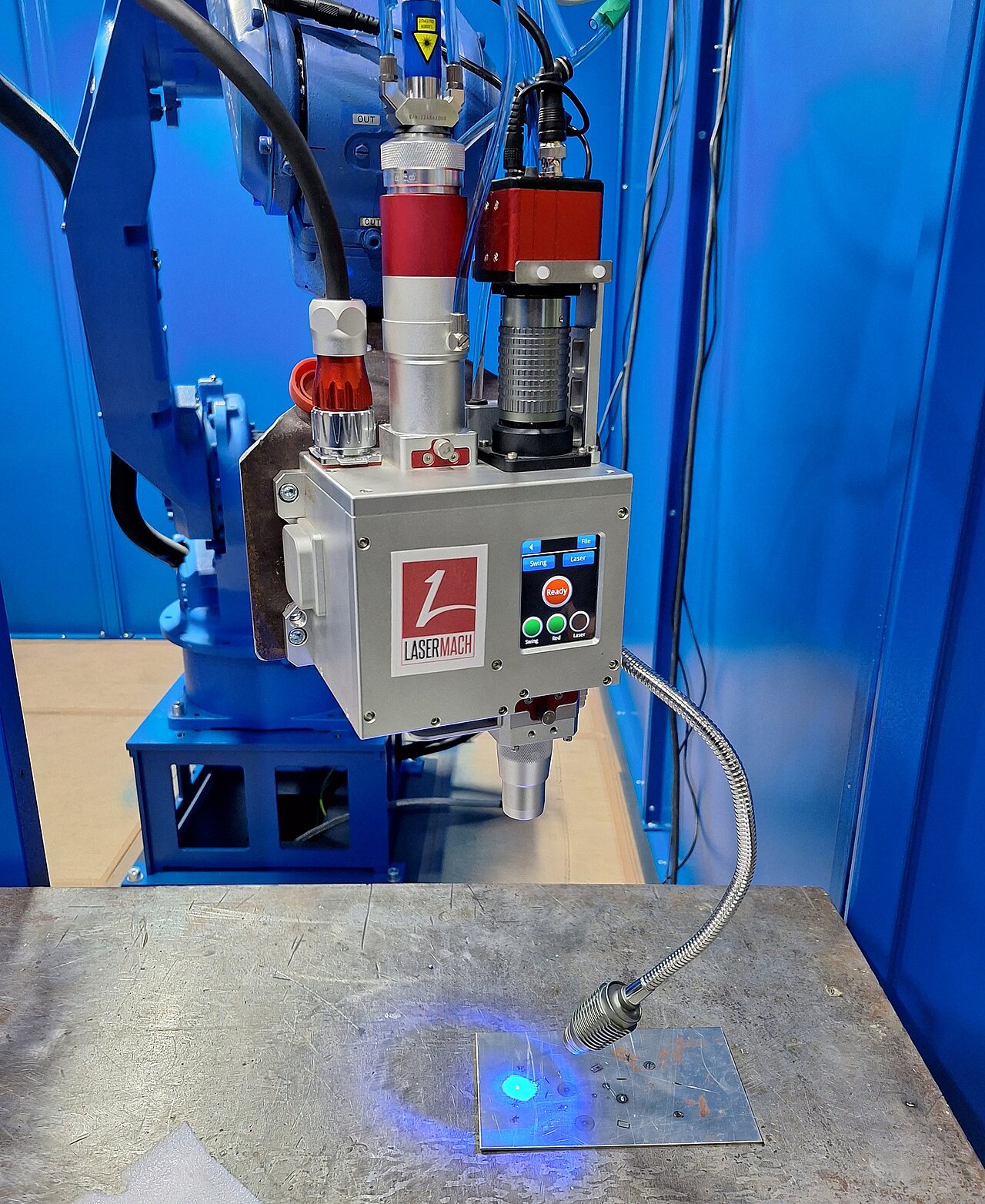
INTELLIGENT WELDING
ROBOTIC WELDING IS A WORTHWHILE INVESTMENT. AND NOT JUST IN SERIES PRODUCTION!
Faster and more precise welding—this is made possible thanks to our R6 series with various auxiliary systems. In combination with robot control, they all support the welder in their work, helping to make the production process as efficient as possible.
This not only saves time and minimizes errors, it also means that welds can be reproduced in the desired quality at any time—without the need for manual fine-tuning. What’s more, they can withstand the greatest loads and meet the highest demands thanks to their outstanding design.
The main differences between robots and cobots
To emphasize the differences between robot and cobot, the abbreviation “cobot” was coined to insist on the collaborative nature of those devices.
While a robot performs a task without human control, a cobot performs tasks in collaboration with human workers. The cobot differs from industrial robots in the way that operators can work safely close to it without fences. That opens many possibilities, like being able to hand-guide its movements or to work in tandem.
However, the comparison between cobot and robot is broader.
Here are the main points of difference between robot and cobots :
Safety
Collaborative robot’s main advantages are about safety. Besides their lightweight and design, they provide high-end sensing features to prevent, detect and avoid collisions. That includes safe stop systems, accurate force sensing, and space-delimitation features. Those features are rarely included in standard industrial robots, since they work in closed working cells.
Flexibility
A cobot’s main difference over an industrial robot is flexibility. Their lightweight design makes them easy to deploy, while they are fast and easy to program. As a result, they can quite quickly adapt to line changes and multiple part shapes. In contrast, traditional robots are heavy, hard to move, and require complex programming, so they are set up for one and never-changing task.
Accessibility
Collaborative robots also stand out for their cost and accessibility, especially for modest manufacturing businesses. Cobots help improves the productivity of SME’s workers by handling precise tasks at a low cost. Workers can deploy and teach cobots their work without external help. They are also more easily accepted among workers, as they feel they are more an ally of their work than a threat to their job. They benefit from them to improve their work condition and satisfaction. So they are easy to implement on existing processes.
Industrial robots, on the other hand, are quite expensive to purchase and require long and energy-intensive integration processes. As a consequence, SMEs can’t really afford them and can’t expect decent ROI from their investments.
Sensing capabilities
Standard Industrial robots hardly feature other perception capabilities than vision. A cobot, by contrast, can rely on a variety of sensing technologies. It can sense force and motion provided by workers, and can support a wide range of high-end vision end-effectors. On the one hand, force and torque sensors enable them to adapt their movements during changing tasks. On the other hand, vision end-effectors can help cobots detect and select changing parts on moving conveyor belts. Workers can quite easily train their cobots to handle high mix part feeding flow.