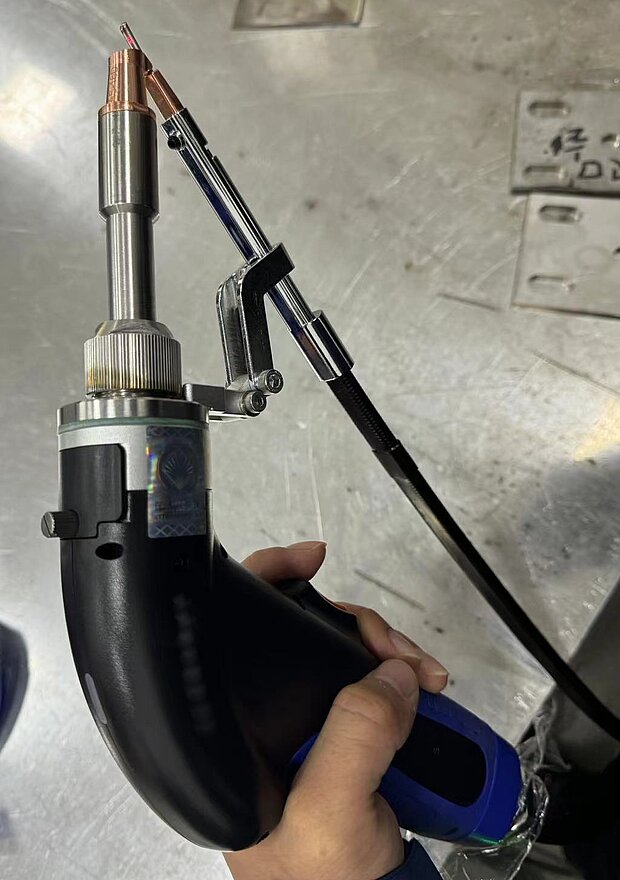
Laser Welding Wire-Feeder-System
COLD WIRE FEED IN COMBINATION WITH LASER WELDING
High-precision wire feeding is particularly important in laser welding and laser brazing. The smallest tolerances in the wire speed immediately result in interruptions or excesses in the seam pattern. The PhotonWeld full digital wire feeding system guarantees a highly precise and fast wire feeding and is therefore used in most of all mechanical production. Most of the Visible seams are welded so cleanly that they can be painted directly.
The use of cold filler wire generally results in a 10% to 20% decrease in welding speed, for a given laser power, to compensate for the laser energy that has to be used to melt the wire. This speed reduction can be counteracted by an increase in laser welding power.
In particular instances, the addition of filler wire might be necessary to:
- Improve the joint fit-up tolerance of welding laser
- Reduce solidification cracking of the weld
- Modify the chemical composition or the microstructure of the weld metal to obtain suitable mechanical specifications
- Achieve multi-pass welds or fill a grooved joint preparation
The use of cold filler wire generally results in a 10% to 20% decrease in welding speed, for a given laser power, to compensate for the laser energy that has to be used to melt the wire. This speed reduction can be counteracted by an increase in laser power (if available), the use of a hot (resistance heated) wire feed.
4-roller precision wire feed.
The 4-roller precision wire feed with tacho-controlled feed motor ensures precise wire feeding.
Digital speed control.
Ensures precise and reliable cold wire feeding while welding
Direct connection to the power source.
Simply connect the Lasermach Feed to your PhotonWeld A-PRO welding unit using the dedicated cable. This will exchange all relevant information and allow integrated control between your PhotonWeld welding unit and the automatic wire feed.
Standard with digital wire feeder
highest productivity for the laser welding pros.
Laser Automatic Wire Feeder - Filler Wire Feeding Machine Digital Controlled is for us a standard
For Wire Type: Stainless Steel, Carbon Steel, Alumimum, Alloy, cupper, etc = We use standard welding wires on standard rolls
The cold wire feeder for Laser Welding by Lasermach offers highest productivity for the laser welding pros.
The lasermach Feed wire feed for Laser welding units ensures superior quality and high speed Laser welding with perfect precision. For this purpose, the automatic wire feed has a fully digital control, a tacho-controlled feed motor, and a 4-roller high-precision feed for precise wire feeding.
The Lasermach cold wire feeder ensures fool-proof feeding and reliable results without spatter in combination with the Laser welding unit when the maximum deposition rate is required in Laser welding. It is ideal for all laser welding tasks in which a filler metal is essential.
How To Choose the Right Feeder for laser Weldiing?
Choosing the right wire feeder for the job does play an important role in reducing unnecessary downtime for addressing issues associated with poor wire feeding.
Choosing the right wire feeder for laser Welding
Having the right wire feeder for the job is more important than many realize. Not only it does help improve the weld quality, but it can also lower costs and increase productivity. The right wire feeder ensures that laser welding operators spend more time welding than they do addressing issues associated with poor wire feeding, which inevitably lead to unwanted downtime.
The first factor to consider when selecting the best wire feeder is how often it will be in use, as the feeder needs to be durable enough to handle the job. It is equally important to factor in the laser welding gun type and weight, as well as the type and size of wire being used. There are three main categories of wire feeders to choose from: basic, intermediate and advanced.
⇒ Basic wire feeders
Basic wire feeders feature one main control to adjust the wire feed speed and are typically the most cost-effective. They do not include meters to indicate how much wire is passing through or to display the exact wire feed speed. They also do not usually feature remote control. Generally, basic wire feeders use a two-roll drive system, which works well with welding guns up to 2~3 meter long. They also may use a four-roll drive system for welding guns with wire length higher than 3m long. Since they have a less powerful motor, they are best suited for wire that is smaller diameter and shorter length.
⇒ Intermediate wire feeders
Intermediate wire feeders usually have four-roll drive systems. They are available in single and dual models that hold either one or two spools of wire. These four-roll drive systems grip the wire better and can therefore push larger wire than a simple, two-roll drive system. Some intermediate feeders can even push wire up to 2.5 mm diameter.
Intermediate models can be used with longer guns, up to 6 meter, and typically have more advanced features. Most models include digital meters that allow welding operators to see the precise wire feed speed and voltage. This voltage control can boost productivity by allowing welding operators to adjust the voltage at the wire feeder rather than at the power source, which could be placed many meters away. In addition, intermediate models typically have a run-in control that allows the wire to feed into the starting melting pool very slowly for smoother starts.
⇒ Advanced wire feeders
Advanced wire feeders, like our PhotonWeld A-Pro is equipped, offer operators the most control over how they start and stop the wire, and how much speed it has. They typically feature enhanced displays that allow a welding operator to accurately view a variety of settings. Advanced wire feeders are ideal for the most critical manufacturing jobs, and they have evolved to accommodate multiple materials.
Advanced wire feeders also tend to have program locks, limits and ranges, which helps keep welders within certain operating windows. In addition, they often have pre-flow, a start parameter, a crater parameter and post-flow. Pre-flow helps ensure operators have good gas coverage and reduces the risk of porosity at the start of the weld. The run-in parameter helps bring the wire in slowly to ensure smooth starting. At the end of the weld, the end or crater parameter and post-flow parameter minimize the opportunity for craters or porosity to appear.
Feeding Wire in Laser Welding Applications
Wire feeding in laser metal joining applications is all about precise wire positioning relative to a laser beam and accuracy in wire feeding speed.
Wire feeding system layout and configuration are key parts in ensuring a successful application that makes the communication between user, integrator, and equipment manufacturers, at early project stages, highly important for a laser metal joining cell performance.
Certain laser metal joining processes, such as brazing or sometimes welding for instance, involve filler metal heating to the point where it can change from a solid to a liquid state, which allows it to flow and create a bond once hardened. The metal is delivered in the form of wire.
Wire can vary vastly in laser metal joining applications. The most general, or common, types you will see are soft wires (aluminum) and hard wires (steel, silicone bronze). Based on the wire type you are working with and the wire feeding distance, your system will be configured differently.
When considering the important factors of what makes your laser welding operation successful, think about precision and performance.
Laser beams are extremely precise, typically between one to three millimeters in diameter depending on the process. You need to lead wire directly into the spot without any deviation. Anything as little as 0,1 millimeters off can potentially have negative effects on the quality of the weld.
Accuracy of wire feed speed into a process is also very important. Typically, the accuracy is defined as a percentage of a wire feed speed set (required) value. Wire feeding system specifications typically show from one to five deviation from a set value as their accuracy success rate. Deviations above 5% from the wire feed speed set value will have negative effects on joints quality and appearance because such laser metal joining processes require exact amounts of wire for integrity, and in case of visibility for appearance joints. This is why the requirements to joints unity and appearance are very high with this application type.